Hydraulic oil seals play a crucial role in the efficient operation and maintenance of hydraulic systems across numerous industries. Responsible for preventing fluid leakage and contamination, these components ensure the longevity and reliability of machinery. A deep understanding of the various types of hydraulic oil seals can significantly impact system performance, maintenance costs, and operational efficiency.
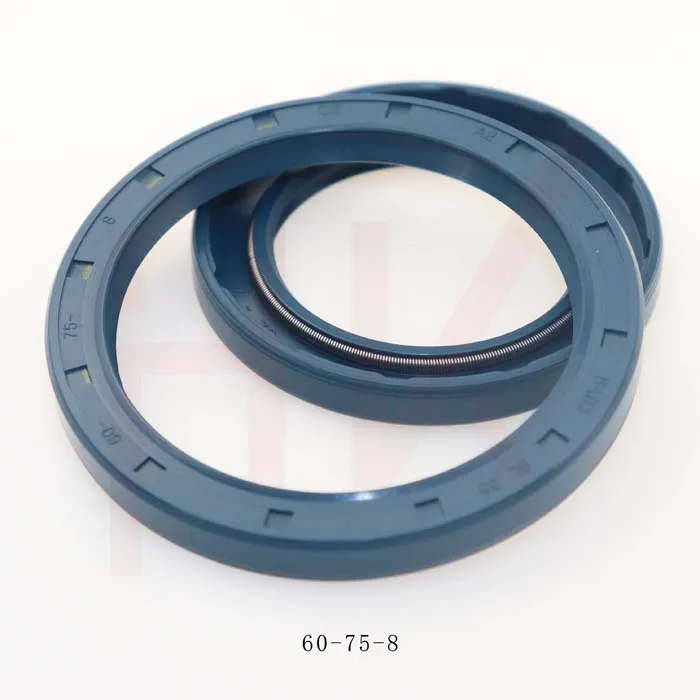
Category Breakdown of Hydraulic Oil Seals
The selection of the right hydraulic oil seal depends heavily on the specific requirements of the machinery and operational conditions. Key types include

1. Piston Seals These seals are integral in preventing hydraulic fluid from leaking past the piston in a hydraulic cylinder. By ensuring optimal motion control, they enhance the performance of hydraulic cylinders. Piston seals must be resilient to high-pressure environments and often come in materials like PTFE, rubber, and polyurethane.
2. Rod Seals Positioned at the open end of hydraulic cylinders, rod seals keep hydraulic fluid from escaping. They are subject to significant pressure and friction, making durability essential. Effective rod seals, often made from nitrile rubber, polyurethane, or fluoroelastomers, maintain the integrity of the hydraulic system.
3. Wiper Seals (Scrapers) Dust and contaminants can enter hydraulic systems where the rod extends and retracts. Wiper seals, therefore, act as a barrier, ensuring the system remains clean and free from debris. Maintaining these seals reduces wear and tear on equipment.
4. Buffer Seals These seals provide an additional layer of protection by absorbing excess pressure spikes that primary seals may not handle. They help in prolonging seal life and preventing fluid leakage, contributing to system reliability.
5. Rotary Seals Used in applications where rotation occurs, such as in hydraulic motors or within steering systems, rotary seals protect against contamination and prevent fluid leakage during rotational movements.
Material Considerations for Optimal Performance
Choosing the appropriate material for hydraulic oil seals is critical for their performance and longevity. Here’s a closer look at commonly used materials
hydraulic oil seal types
- Nitrile Rubber (NBR) Known for its excellent resistance to petroleum-based fluids, nitrile rubber is widely used for its affordability and effectiveness in moderate temperature ranges.
- Polyurethane (AU) This material stands out for its exceptional abrasion resistance and durability, making it suitable for high-pressure environments.
- Fluoroelastomers (FKM) Valued for their strong chemical resistance and ability to perform in high temperature environments, fluorocarbon seals are ideal for demanding applications.
- Polytetrafluoroethylene (PTFE) Offering low friction and chemical compatibility, PTFE is an excellent choice for use in high-speed applications that generate heat and friction.
Strategic Selection and Installation
When selecting hydraulic oil seals, one must evaluate the operational environment, exposure to chemicals, temperature extremes, and pressure conditions. A precise understanding of these variables allows for the selection of seals that not only fit design specifications but also enhance operational efficacy.
Proper installation is equally crucial. Incorrectly installed seals can lead to premature failures and costly downtime. It's essential to ensure the compatibility of the seal with its corresponding groove and check for any nicks or damage before installation.
Maintenance and Replacement
To maintain the efficacy and longevity of hydraulic oil seals, regular inspections and preventative maintenance are vital. Monitoring temperature changes, lubricant conditions, and pressure levels can prevent unexpected seal degradation. When replacement becomes necessary, opting for high-quality seals from reputable manufacturers can reduce installation errors and prolong equipment life.
Hydraulic oil seals might be small components, but their impact on system operation is substantial. By thoroughly understanding their types, materials, and applications, one can significantly enhance system reliability, reduce downtime, and lower maintenance costs. Keeping abreast of the latest developments in seal technology, materials, and design will ensure that you remain at the forefront of industry best practices.