The world of hydraulic systems relies heavily on various components to function efficiently, and one of these critical components is the hydraulic oil seal. Oil seals play a crucial role in ensuring the longevity and efficiency of hydraulic systems by preventing fluid leakage and blocking contaminants from entering the system. Selecting the right material for hydraulic oil seals is a critical decision that can impact the overall performance and reliability of hydraulic machinery. This article delves into the essential materials used in hydraulic oil seals, focusing on their unique properties, applications, and benefits to provide an authoritative guide on the subject.
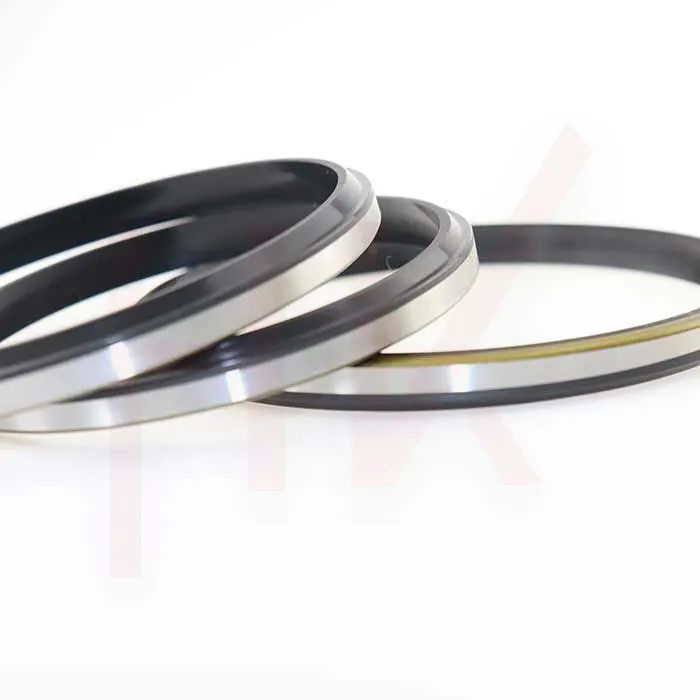
Hydraulic oil seals are available in various materials, each offering distinct advantages depending on the specific requirements of the hydraulic system. The choice of material impacts seal performance, compatibility with hydraulic fluids, temperature resistance, and overall durability. Below are some of the most popular materials used in hydraulic oil seals
1. Nitrile Rubber (NBR) Recognized for its excellent oil resistance, nitrile rubber is one of the most commonly used materials for hydraulic oil seals. Its ability to withstand temperatures ranging from -40°C to 120°C and its resistance to wear make it an ideal choice for many applications. However, while NBR is resistant to petroleum-based oils and fuels, it is not suitable for applications involving phosphate ester-based fluids or glycol-based brake fluids.
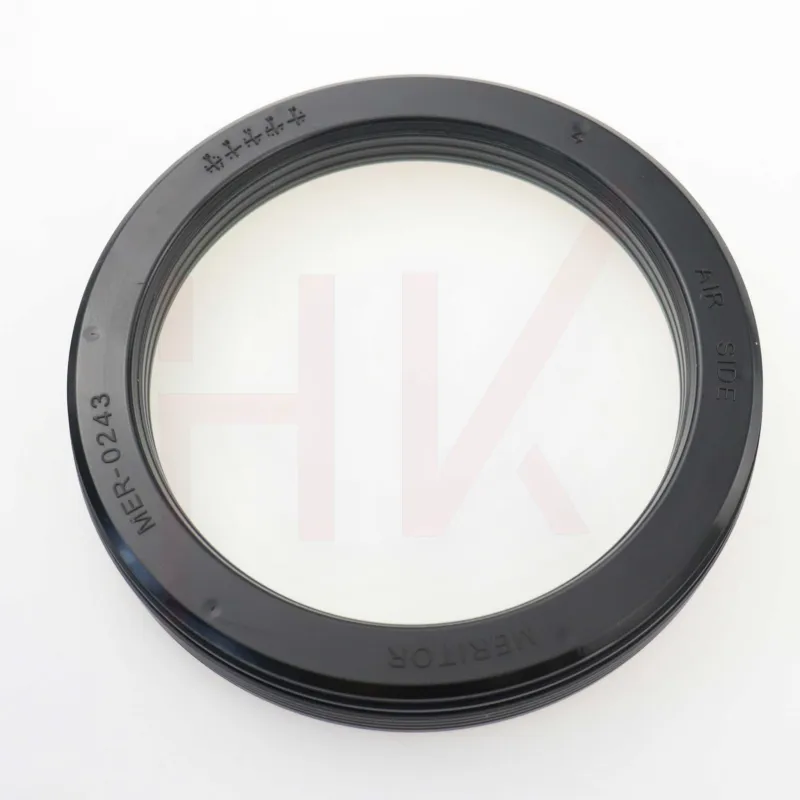
2. Fluorocarbon (Viton®) For applications requiring enhanced chemical and temperature resistance, fluorocarbon offers remarkable stability. These seals can withstand temperatures up to 200°C and resist degradation from many solvents and chemicals, making them suitable for aerospace and automotive industries where both high temperatures and harsh chemicals are prevalent.
3. Polyurethane (PU) Known for its exceptional resistance to abrasion and tear, polyurethane seals provide superior strength and resilience in dynamic applications involving high-pressure and high-speed movements. While polyurethane is more rigid than rubber compounds, its resistance to oily and greasy environments, as well as its operational temperature range of -30°C to 80°C, makes it a reliable choice for hydraulic systems.
hydraulic oil seal material
4. Silicone Rubber Offering superior flexibility and resilience across a wide temperature spectrum (-50°C to 230°C), silicone seals are excellent for applications subjected to extreme weather variations. They provide good resistance to ozone and UV light; however, they may not perform well in environments requiring interaction with petrol-based oils and must be carefully chosen for appropriate scenarios.
5. Polytetrafluoroethylene (PTFE) With its renowned low-friction properties and resistance to high-temperature and aggressive chemicals, PTFE, commonly known as Teflon, is used in demanding applications where other materials might fail. Its operational temperature breaks traditional limits, ranging between -200°C and 260°C, providing unparalleled performance in challenging conditions such as oil and gas drilling and high-speed rotating equipment.
The choice of material for hydraulic oil seals requires careful consideration of the specific operational environment. The key factors include compatibility with the type of hydraulic fluid used, the operational temperature range, pressure conditions, and the dynamic versus static nature of the application. With advancements in technology, composite materials and innovative solutions are being developed to enhance the performance of hydraulic oil seals even further.
Proper maintenance and regular inspection of hydraulic oil seals are equally crucial in ensuring their performance. Regular checks can help in identifying early signs of wear or damage, allowing timely replacements and avoiding costly system failures. In applications with demanding requirements, these seals must frequently be replaced or maintained according to manufacturer recommendations to secure system integrity.
In conclusion, hydraulic oil seals play an indispensable role in the efficiency and durability of hydraulic systems. By selecting the appropriate seal material tailored to the specific operational circumstances, industries can enhance the performance, reliability, and lifespan of their equipment. Given the broad spectrum of materials available, understanding their unique properties and limitations is vital. This expertise helps in making informed decisions that directly contribute to the optimization of hydraulic system performance. In a landscape where efficiency and uptime are paramount, the right choice of hydraulic oil seal material is not just a technical decision but a strategic advantage.