The world of hydraulic motors is intricate, yet essential for powering countless industrial applications, from mobile equipment to heavy machinery. At the heart of these motors’ efficiency and longevity lies the hydraulic motor seal. This component is indispensable in maintaining system pressure and preventing leaks and contamination. However, over time, seals wear down, leading to diminished performance or even equipment failure. Replacing a hydraulic motor seal is not just routine maintenance but a crucial task to ensure the safety, performance, and durability of the machinery.
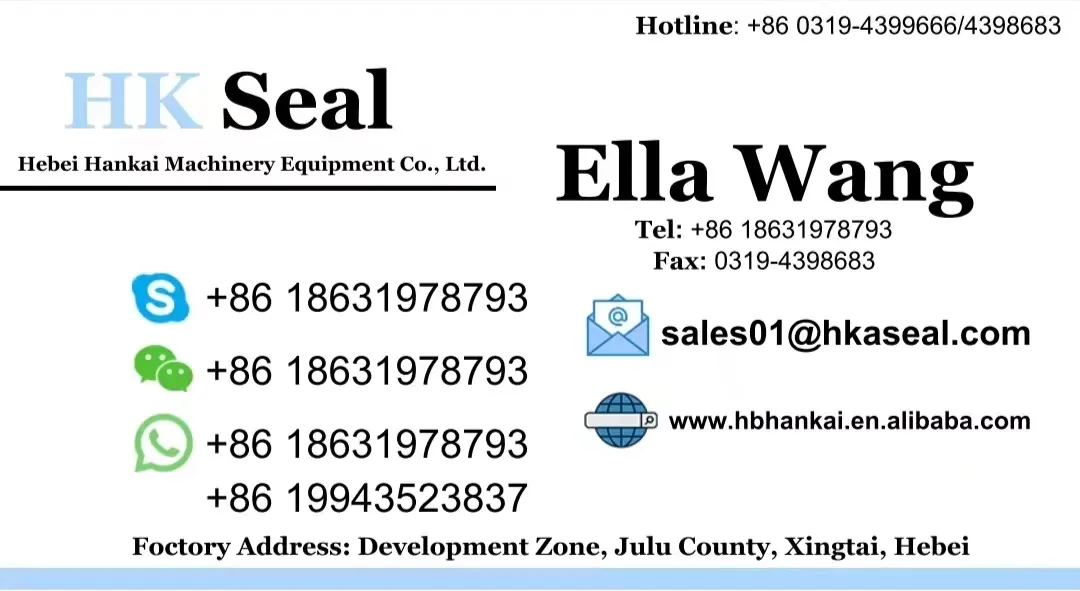
An in-depth understanding of hydraulic motor seal replacement requires one to delve into the intricate details of how these systems function. When a seal wears out, it becomes evident through symptoms such as fluid leaks, significant pressure drops, or irregular motor motion. Ignoring these signals can lead to catastrophic failures, spiraling into costly repairs and downtime.
To begin the replacement, first ensure the work area is clean, organized, and equipped with the necessary tools. This minimizes contamination—an adversary for hydraulic systems. Isolate the motor from the hydraulic system by disconnecting it safely, preventing fluid from spilling during the process. Proper lockout and tag-out (LOTO) procedures are crucial to ensure safety while working.
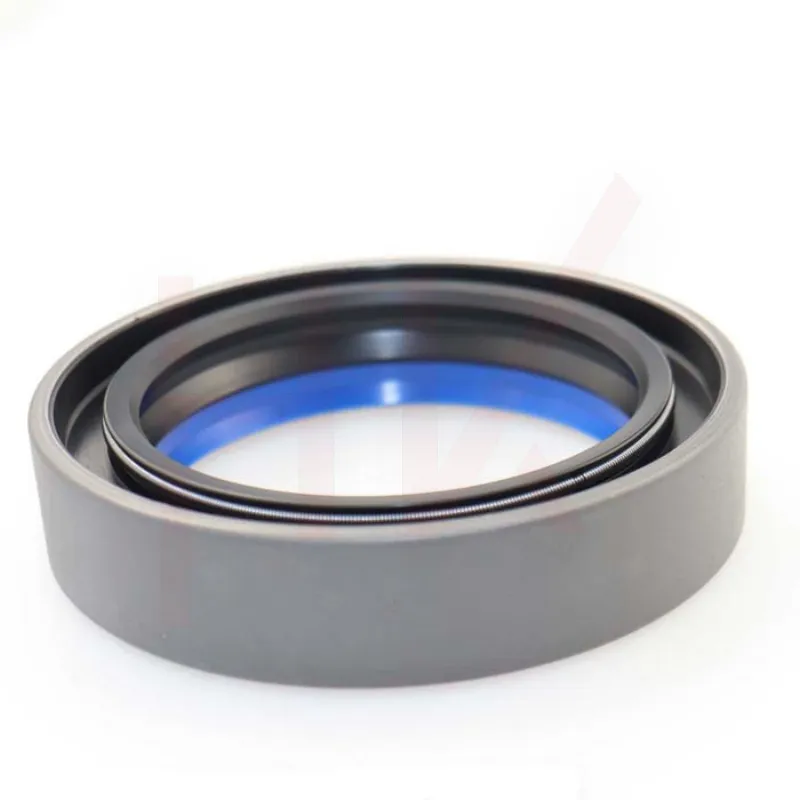
Dismantling the motor involves careful disassembly, noting each part's location and orientation. Taking photographs can offer a visual guide, simplifying reassembly. As the motor is opened, inspect the seals carefully. Identifying the type of seal is crucial; they come in various materials like nitrile rubber, Viton, or Teflon, each with specific properties suited to different applications and environments.
Once the faulty seal is identified, assess the housing and surrounding components for wear or damage. It's prudent to clean the area meticulously, ensuring no debris or old seal remnants remain. Any abrasions or scratches in the housing can compromise the integrity of the new seal, leading to premature failure.
The installation of the new seal demands precision. Lubricate the new seal lightly, allowing for a smoother fit without excessive force, which can cause damage. Gently seat the seal using the appropriate tools, ensuring it is evenly placed without any deformation. Misalignment can cause leaks or reduce the seal’s lifespan.
hydraulic motor seal replacement
Reassembly requires as much attention to detail as disassembly. Ensure each component is cleaned and re-lubricated if necessary. As you piece the motor back together, torque specifications should be adhered to, ensuring all bolts and components are secured properly to prevent future issues.
Testing the motor post-assembly is essential to confirm the efficacy of the replacement. Reconnect the motor to the hydraulic system gradually, monitoring for leaks or irregularities. Observing the system under pressure provides immediate feedback on the seal's installation success.
One cannot underscore enough the importance of using quality seals from reputable manufacturers. Investing in high-grade materials often translates to longer intervals between maintenance sessions, reducing the potential for unexpected downtimes and associated costs.
For those tasked with maintaining hydraulic systems, continuous education and staying abreast of industry advancements in materials and seal technology is vital. Manufacturers continually improve their product offerings, developing seals with enhanced performance characteristics and longevity.
Moreover, respecting the expertise of seasoned technicians can provide invaluable insights during such maintenance tasks. Their experience in nuanced situations can often point out potential problems before they arise, safeguarding both machinery and personnel.
In conclusion, hydraulic motor seal replacement, while seemingly straightforward, embodies a blend of precision, knowledge, and quality materials. It is not just a procedural task but a pillar of proactive maintenance, ensuring operational reliability and efficiency. By approaching the replacement with diligence and an informed mindset, one can prolong the life of hydraulic machinery, maintaining safety standards and optimizing productivity. Such practices underscore the tenets of expertise, trustworthiness, and authoritativeness, ensuring that each aspect of the process is grounded in reliability and excellence.