Choosing the right hydraulic motor oil seal for an application is a crucial step towards ensuring the longevity and efficiency of hydraulic machinery. A hydraulic motor oil seal, often an overlooked component, bears the burden of maintaining system integrity by preventing fluid leakage and contamination, which can otherwise lead to costly downtimes and repairs.
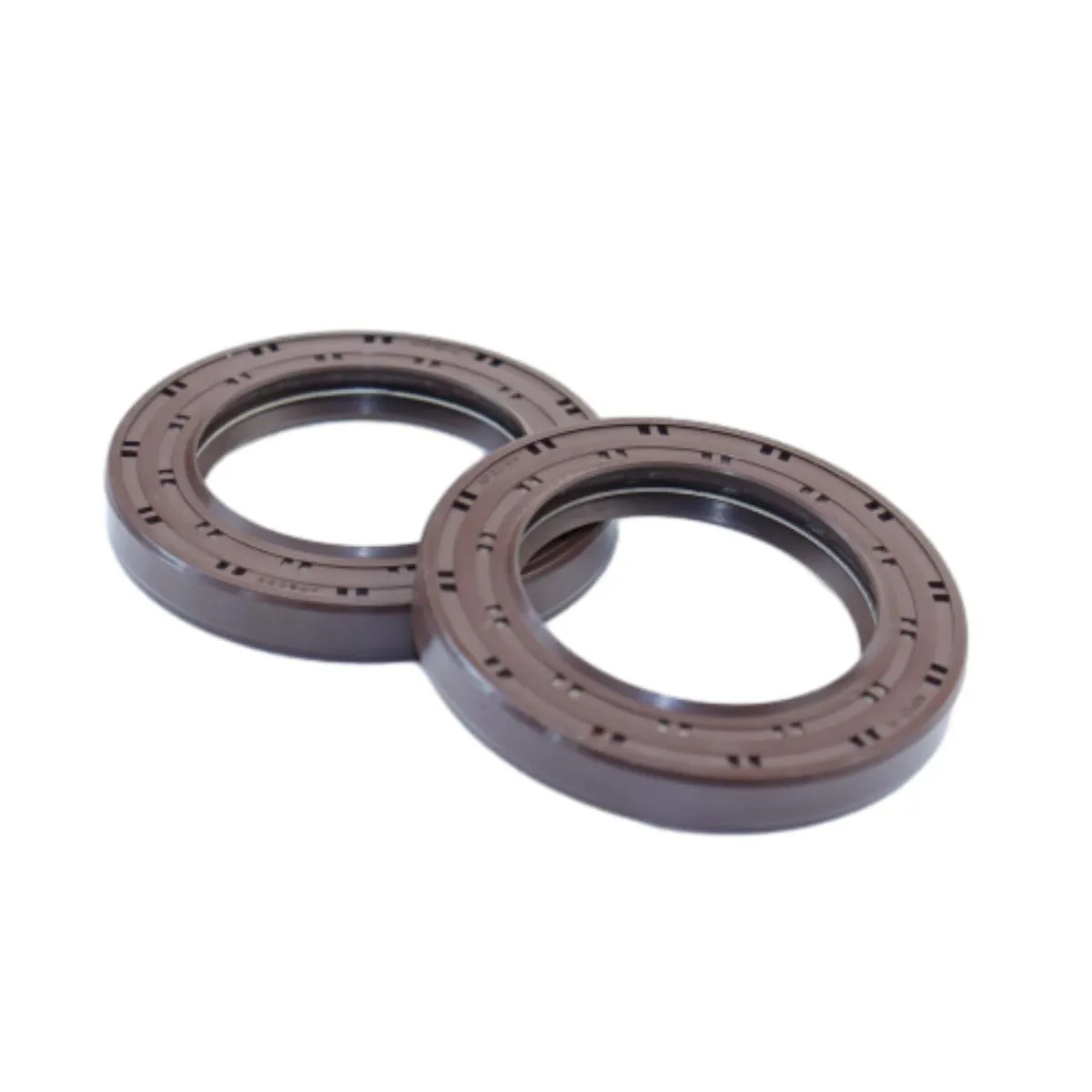
Understanding the complexities of hydraulic systems can help one appreciate the role of an oil seal. Picture a hydraulic motor; it is a form of rotary actuator that uses hydraulic pressure and flow to produce mechanical motion. In essence, the hydraulic oil seal in such a system acts as a defender, keeping the crucial components immersed in high-pressure oil while keeping contaminants and debris at bay. Ensuring a perfect seal in these systems requires precision-engineered components, expert knowledge, and a dedication to understanding each application's unique needs.
The importance of selecting the correct material for the oil seal cannot be overstated. Common materials include nitrile rubber, Viton, silicone, and polyurethane, each offering distinct properties suited for different environments and operational stresses. Nitrile is popular for its affordability and resistance to petroleum-based oils. Viton seals are invaluable in high-temperature applications due to their superior heat resistance, whereas silicone offers low-temperature performance. Polyurethane seals are ideal for environments where abrasion resistance is critical. Selecting the appropriate material not only enhances performance but also extends the lifespan of both the seal and the machinery.
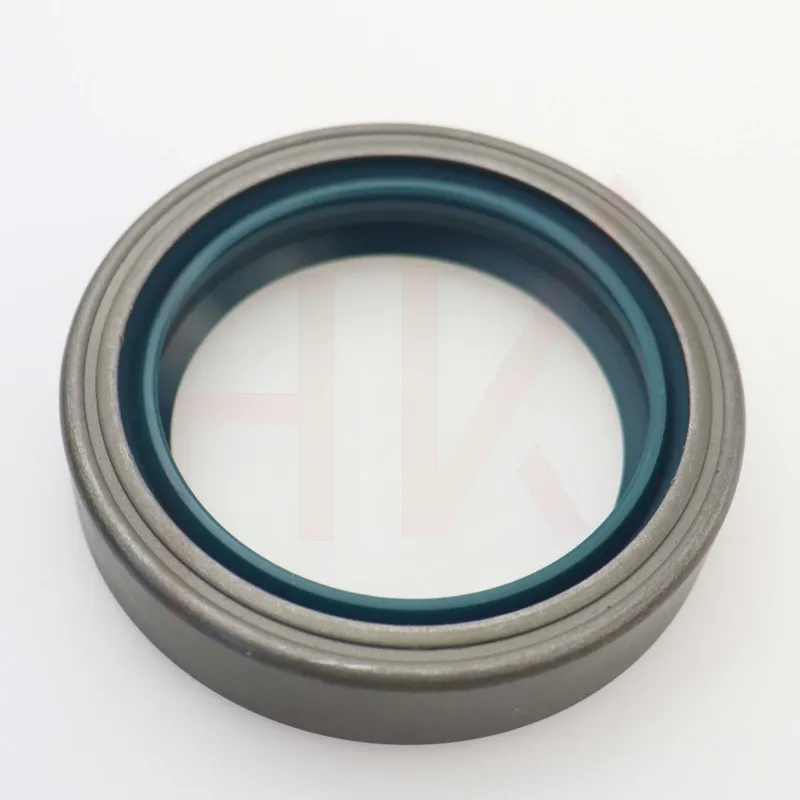
Expertise in the design of hydraulic oil seals also plays a pivotal role. Seals must be engineered to accommodate variables like shaft misalignment, thermal expansion, and pressure fluctuations, all while maintaining flexibility and resilience. Experts in hydraulic systems often underscore the necessity of precision in seal lip design and the importance of choosing the correct size and fit. A seal that is too tight can generate excess friction and wear, while a loose seal fails in its primary function of containment.
hydraulic motor oil seal
Building authority in the hydraulic components industry requires staying ahead in research and development. Innovations in oil seal technology, such as those seen with the integration of advanced composites and hybrid materials, are enhancing the performance capabilities significantly. These advancements promise reductions in friction, lower energy consumption, and greater resistance to a broad spectrum of chemicals, setting new benchmarks in the field.
Trustworthiness and reliability of a manufacturer can directly influence a customer's decision to purchase. High-quality life testing and rigorous quality control measures help assure that the product will withstand operational demands and meet the performance expectations. Certifications from industry-standard organizations provide additional assurance of quality and reliability.
Real-world experience consistently confirms that a well-chosen hydraulic motor oil seal improves machinery efficiency, reduces energy consumption, and lowers maintenance costs by preventing leakage and contamination. Industry veterans often share success stories of how certain seal designs have drastically improved their operational output, offering testimonials to the benefits of quality seals.
The continuous evolution in hydraulic fluid technology and machinery demands a parallel progression in sealing solutions. Companies eager to maintain a competitive edge must continually adapt and optimize their offerings, drawing from both direct user feedback and industry trends. Through strategic product innovation and commitment to excellence, the journey towards enhancing machine performance with the right hydraulic motor oil seal continues unabated.