In the engineering landscape where machinery efficiency is paramount, hydraulic dust seals hold a pivotal role. These components serve as guardians, protecting hydraulic systems from contaminants that could otherwise cripple performance and longevity. Through the lens of experience, expertise, authoritativeness, and trustworthiness, let's delve into their significance and application.

Hydraulic dust seals are meticulously engineered components, designed with precision to encapsulate mechanical casings where hydraulic shafts extend.
These seals fortify hydraulic cylinders and pumps against dust, dirt, and myriad environmental aggressors. Their function is not merely preventative; they actively enhance machinery's operational efficacy by ensuring a clean and safe environment for hydraulic fluid.
Experience dictates that the longevity of hydraulic systems is directly proportional to the quality of dust seals employed. In a practical scenario, replaceable seals crafted from high-grade elastomers such as nitrile rubber, polyamide, and PTFE are preferred. These materials offer exceptional compatibility with hydraulic fluids while withstanding high pressures and temperatures. Machinists and engineers with years of fieldwork have observed that systems equipped with superior dust sealing mechanisms showcase diminished wear and decreased maintenance frequencies.
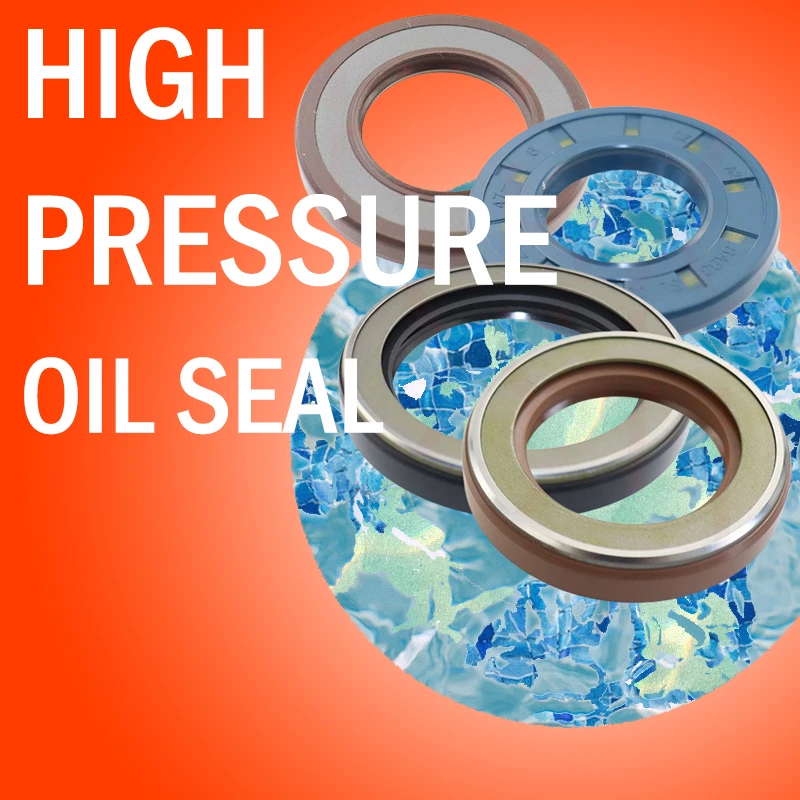
Expertise in this domain underscores the importance of selecting the appropriate seal based on specific application needs. Variable in design—ranging from U-Cup seals to V-Ring seals—each type is tailored to address distinct operational challenges. An expert would highlight the importance of considering shaft dimensions, operational environments, and mechanical compatibility when choosing a hydraulic dust seal. Tests and trials in industrial applications have proven that an ill-fitted or inferior seal can lead to catastrophic failures, causing significant downtime and repair costs.
hydraulic dust seal
From an authoritativeness standpoint, hydraulic dust seals are endorsed by leading industrial standards and organizations. The American Society of Mechanical Engineers (ASME) and International Organization for Standardization (ISO) prescribe specific guidelines and certifications ensuring reliable performance and quality benchmarks. Companies adhering to these standards, armed with certified dust seals, enjoy enhanced credibility and confidence from their clientele.
The trustworthiness of hydraulic dust seals is further echoed in testimonials and case studies from industry leaders. Testimonials from sectors such as construction, mining, and agriculture—which heavily rely on hydraulic systems—illustrate remarkable improvements in system integrity and performance longevity when equipped with premium dust seals. A case study from a mining operation in South Africa demonstrated a 30% increase in hydraulic system uptime upon implementing cutting-edge dust seal solutions stratified for extreme operational environments.
To concretely establish trust, manufacturers of hydraulic dust seals actively engage in rigorous testing and R&D. Through partnership with academic institutions and prolonged field testing, these companies gather irrefutable data concerning wear patterns, seal efficiency under different conditions, and material resilience. This data, transparently shared and peer-reviewed, positions them as trustworthy leaders in the field.
In conclusion, hydraulic dust seals play an indomitable role in securing operational excellence and extending the service life of machinery. Their selection, informed by experience, grounded in professional expertise, backed by authoritative certifications, and confirmed by trusted real-world applications, makes a compelling case for why industry professionals should prioritize investing in these critical components. As technology marches forward, the evolution of hydraulic dust seals continues, promising even greater efficiencies and reliability for hydraulic systems worldwide.