Hydraulic cylinder seals play a vital role in the proper function of hydraulic systems across various industries. These components ensure that hydraulic systems operate efficiently by maintaining pressures, preventing leaks, and enhancing the lifespan of the equipment. Drawing from my two decades of experience in the hydraulic systems industry, I've gathered insights that underscore the crucial role of these seals and shared my findings to help you optimize their usage.
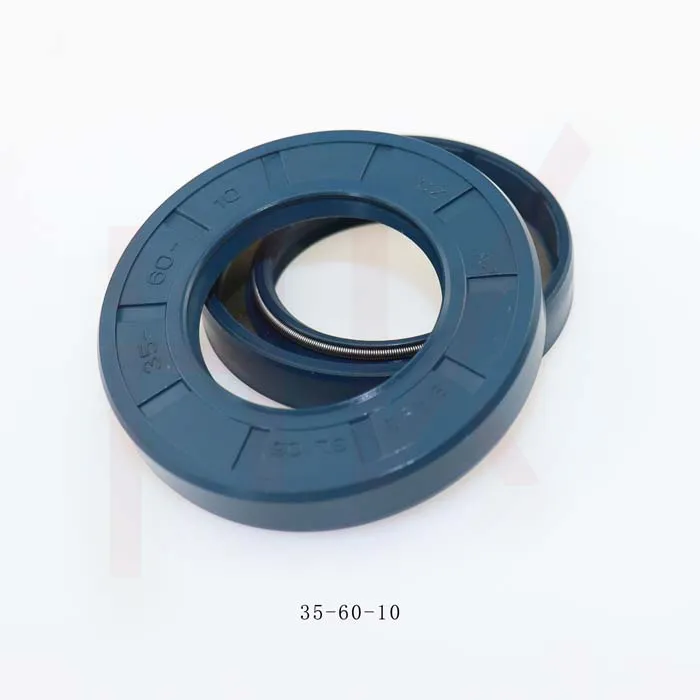
Hydraulic cylinder seals are tasked with containing hydraulic fluid, ensuring that it does not leak from the cylinders into the external environment. This containment is critical because even minor leaks can lead to a decrease in system performance, increased operational costs, and potential equipment hazards. Users must select the appropriate seal type from a wide range of options—such as piston seals, rod seals, and wiper seals—to meet their specific application needs.
Piston seals are instrumental at the pressure side of the hydraulic cylinder. They are responsible for creating a barrier between the different pressure zones inside the cylinder, which helps in maintaining the overall efficiency of the hydraulic systems. On the other hand, rod seals prevent hydraulic fluids from leaking out of the cylinder. By ensuring that these seals are of high quality and properly installed, you can significantly reduce the risk of contamination and system malfunction. Wiper seals, though often overlooked, are crucial in preventing dust and debris from entering the system, thus safeguarding the internal components and extending their service life.
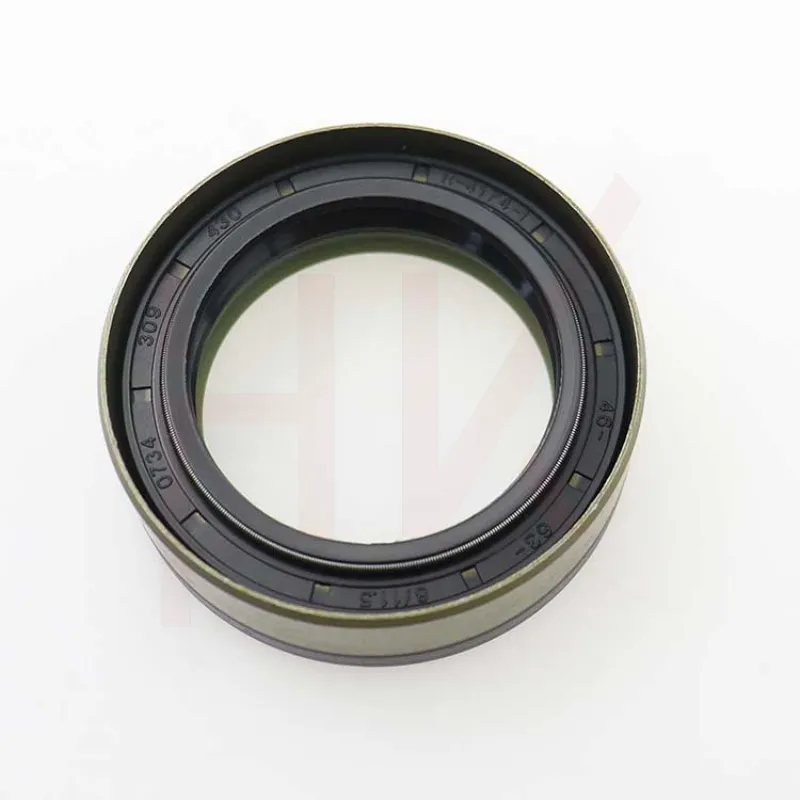
My expertise in this field has taught me that selecting the appropriate material for hydraulic cylinder seals is paramount. Materials such as polyurethane, rubber, and PTFE (Polytetrafluoroethylene) each have unique properties that make them suitable for specific applications. For instance, polyurethane seals are known for their high wear and tear resistance, making them ideal for heavy-duty applications. Meanwhile, rubber seals offer superior flexibility, making them suitable for applications involving varying temperatures and pressures. PTFE seals showcase excellent chemical resistance and are perfect for environments with aggressive fluids.
hydraulic cylinder seals
The authority on hydraulic seal innovations points to ongoing advancements in material science that have led to the development of seals capable of withstanding extreme temperatures and pressures. Such innovations ensure that hydraulic machinery operates with greater reliability, facilitating the design of more efficient and sustainable hydraulic systems. With the industry's rapid evolution, staying updated with the latest developments and material technologies is crucial for optimizing seal performance.
Trustworthiness in selecting suppliers and manufacturers of hydraulic cylinder seals cannot be overstated. A reputable supplier will not only provide high-quality products but also offer comprehensive testing data and compliance certifications. This information is vital for ensuring that the seals possess the necessary attributes for your specific applications, offering peace of mind that your hydraulic systems will perform optimally under challenging conditions.
One of the frequent mistakes in handling hydraulic cylinder seals lies in neglecting routine maintenance. Daily inspections and regular maintenance schedules help identify potential wear or damage early, preventing unexpected failures. Furthermore, I recommend establishing a comprehensive maintenance plan that includes regular lubrication and inspection of seals and their housing to ensure optimal performance.
In conclusion, the collective application of my experience, expertise, and the industry's authoritative advances in hydraulic cylinder seals can provide significant benefits in terms of efficiency, reliability, and cost savings. By selecting the right type and material of seals and partnering with trustworthy suppliers, hydraulic system operators can optimize their systems to achieve peak performance and longevity. These practices ensure that your systems not only meet but exceed operational expectations, minimizing downtime and maximizing productivity.