A hydraulic cylinder is an essential component in many industrial applications, transforming fluid power into mechanical force. Despite its robust construction, even the most durable hydraulic system is prone to wear and tear, which necessitates periodic maintenance and the eventual replacement of seals. Understanding how to conduct a successful hydraulic cylinder seal replacement enhances the functionality of your equipment, minimizes downtime, and extends the service life of the machinery.
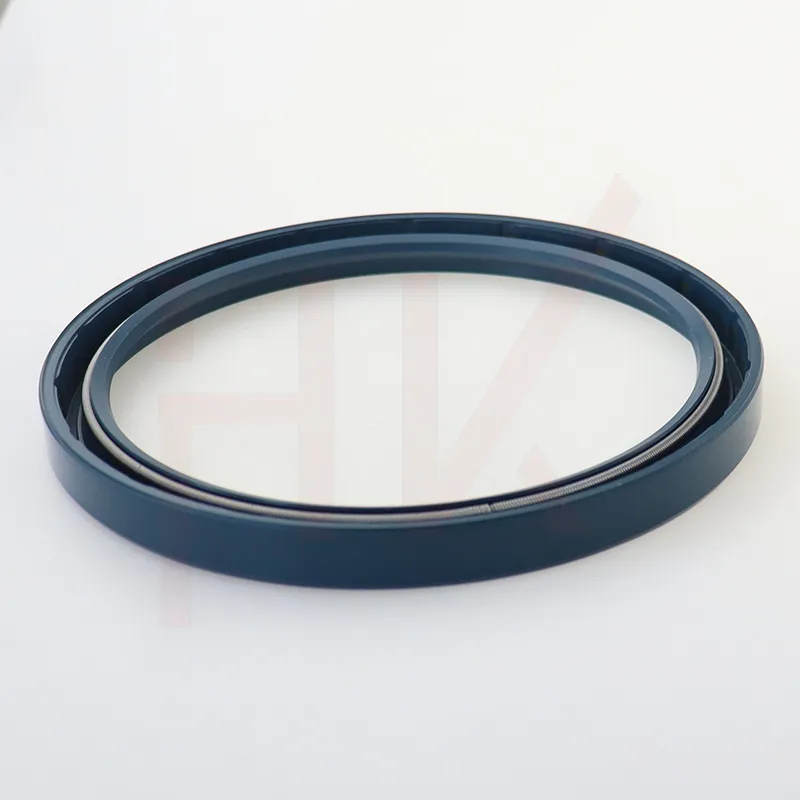
Signs indicating the need for seal replacement often include leaks, loss of pressure, and inefficient performance. Addressing these issues promptly is essential; ignoring them can lead to more significant mechanical failures, which are costly and time-consuming to repair. Thus, the seal replacement is not just a remedy—it is a preventive measure guaranteeing ongoing system integrity.
Expertise in hydraulic systems begins with the acknowledgment of the importance of selecting the correct seal. This choice is guided by several factors the system's operational pressure, temperature, fluid compatibility, and the environmental conditions. Different applications may require varying seal materials; for instance, nitrile rubber offers excellent resistance to oils and hydraulic fluids, while Viton is suitable for higher temperature applications.
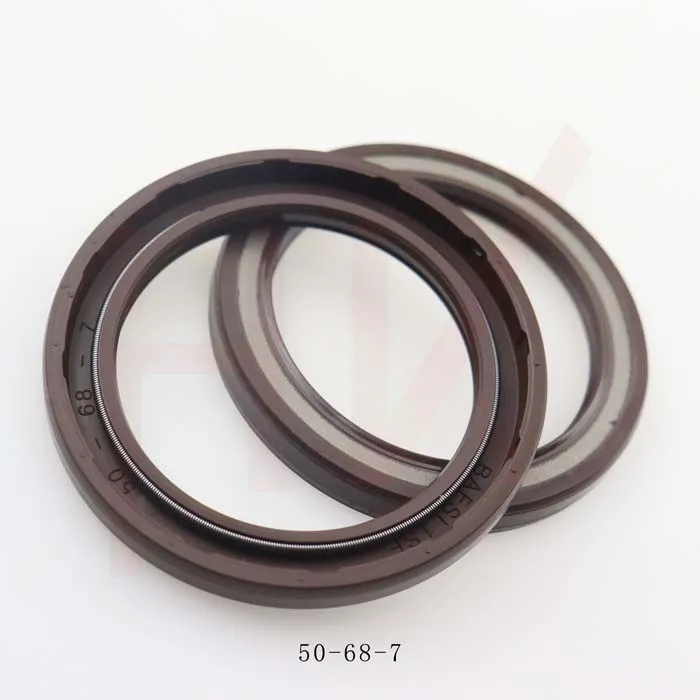
Embarking on the replacement process requires precision and expertise to ensure safety and efficiency. The procedure commences with system depressurization to prevent hazardous fluid
escapes during disassembly. After ensuring all pressure is relieved, the cylinder should be carefully removed from machinery for ease of working. Proper tools are crucial; utilizing the correct spanners, seal picks, and protective gear promotes both safety and accuracy during disassembly.
Thorough cleaning of the cylinder components is fundamental before installing new seals. Residual fluid, debris, and old seal fragments can all compromise the installation of new seals. Inspection of cylinder rods and other components for damage helps identify additional repairs needed or adjustments before proceeding with reassembly. Here, the relevance of high-quality cleaning solutions and lint-free wipes cannot be overemphasized.
hydraulic cylinder seal replacement
With the cylinder cleaned and inspected, one can proceed to install the new seals. Expert craftsmanship is necessary here—seals must be fitted precisely within their designated grooves to function correctly. This step demands not only an eye for detail but also a comprehensive understanding of the system's design. Incorrect seal installation may compromise the entire hydraulic system.
Final reassembly ensures alignment and functionality. This step should be performed meticulously, ensuring all components are securely fastened. Mistakes in reassembly can lead to operational inefficiencies or additional damage. Once reassembled, test the hydraulic cylinder by gradually reapplying pressure and monitoring for leaks or abnormal noise.
Successful testing confirms a properly conducted seal replacement.
Trustworthiness in hydraulic cylinder maintenance is built by consistently following best practices and utilizing quality components. Partnering with reputable suppliers for replacement parts guarantees that the seals fulfill their designed purpose under specified conditions. Comprehensive documentation of the seal replacement process reinforces trust by providing a verifiable maintenance history that can benefit future troubleshooting and audits.
Becoming proficient in hydraulic cylinder seal replacement not only reduces the risk of equipment downtime but also optimizes performance—critical goals in maintaining industrial efficiency. A proactive approach, grounded in experience, expertise, and a commitment to quality, positions operators not merely as technicians but as custodians of mechanical reliability and operational excellence.
In conclusion, hydraulic cylinder seal replacement is a discipline that hinges upon meticulous attention to detail and a commitment to quality. By adhering to best practices and maintaining a culture of excellence, the longevity and efficiency of hydraulic systems can be significantly enhanced, providing measurable value to any industrial operation.