Navigating the intricate world of hydraulic systems requires a nuanced understanding of their components, particularly the seals within hydraulic cylinders. These seals play a pivotal role in ensuring the systems operate efficiently, guarding against leakage, contamination, and mechanical failure. Repairing these hydraulic cylinder seals necessitates a combination of hands-on experience, technical expertise, and a deep-seated knowledge of the latest industry standards and innovations.
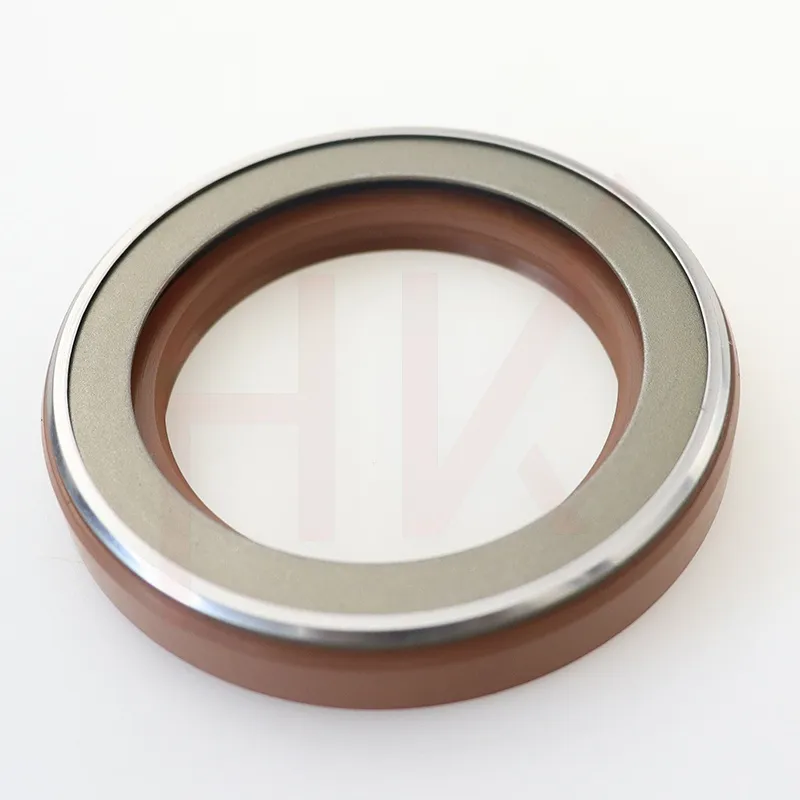
Hydraulic cylinder seals are the unsung heroes in various industrial applications, from manufacturing plants to heavy machinery in construction sites. They are designed to maintain the pressure within the cylinder, thereby ensuring smooth and controlled motion. When these seals wear out or become damaged due to factors such as extreme temperature fluctuations, contamination, or overloading, they can lead to costly downtimes and potentially hazardous working conditions.
The process of repairing hydraulic cylinder seals begins with an in-depth assessment and diagnosis of the issue at hand. Only a skilled technician with years of experience can accurately identify the root cause of the failure. This involves a painstaking inspection of the hydraulic system to detect any signs of wear or damage that may have been overlooked. It is imperative to understand the contextual conditions under which the machinery operates, as this informs the choice of materials and repair techniques.
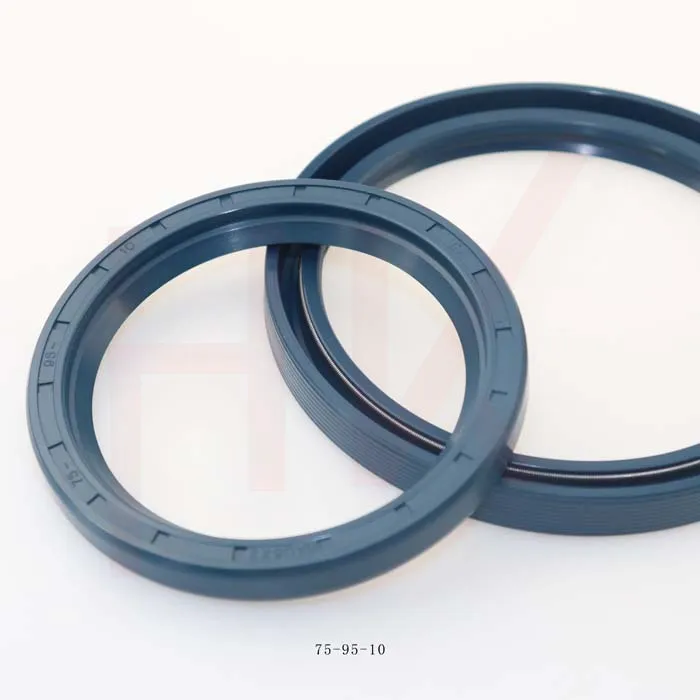
Choosing the right seal for repair is not merely a question of replacing the old one with a new component. It demands an understanding of the materials and designs that best fit the operational needs of the equipment. Seals are made from a variety of materials, including rubber, polyurethane, and PTFE composites, each offering distinct benefits. For instance, rubber seals provide excellent elasticity and resistance to wear, making them suitable for applications involving high-pressure fluids. On the other hand, PTFE seals are lauded for their high-temperature stability and chemical resistance, ideal for challenging industrial environments.
Meticulous attention to detail is essential during the repair process itself. Before replacing the seal, the hydraulic cylinder should be carefully dismantled and each component thoroughly cleaned to remove any residues or debris that could compromise the new seal’s functionality. Preparing the surface by ensuring it is smooth and free of imperfections is crucial. Any surface irregularities could lead to premature seal failure, thus negating the efficacy of the repair.
hydraulic cylinder seal repair
Once the new seal is installed, rigorous testing follows to ascertain the integrity and performance of the repaired system. This testing process often involves simulating operational conditions to verify the repair under stress. Pressure tests and functional cycle tests are effective in ensuring that the seals are seated correctly and performing to specified standards.
The expertise involved in hydraulic cylinder seal repair is continually evolving alongside advances in technology and materials science. Staying abreast of the latest developments is paramount for professionals in the field. Collaborative platforms and professional workshops provide avenues for continuous learning and sharing best practices. Engaging with the community of experts not only enhances an individual's technical capabilities but also reinforces industry trustworthiness and authority.
Hydraulic cylinder seal repair is not a one-size-fits-all task; it requires bespoke solutions tailored to the unique challenges each system presents. By employing a comprehensive approach that combines hands-on experience, technical know-how, and a commitment to quality, one can significantly enhance the operational efficiency of hydraulic systems and extend their lifespan. Such diligence ensures reliability, minimizes downtime, and ultimately promotes safety and productivity.
These principles are not merely theoretical musings but are grounded in verified successes and documented case studies from leading industry practitioners. Whether you are a maintenance technician or an industrial manager, embracing a proactive attitude towards seal maintenance and repair can drive substantial improvements in system performance. Thus, investing in expertise and fostering a culture of continuous improvement stands at the forefront of hydraulic cylinder seal repair excellence.