Hydraulic cylinder seal kits are critical components in the operation and maintenance of hydraulic systems across various industries. The choice of material for these seal kits directly influences the performance, durability, and efficiency of the hydraulic cylinders they are used in. When selecting the right material, understanding its properties and the specific demands of your application is crucial.
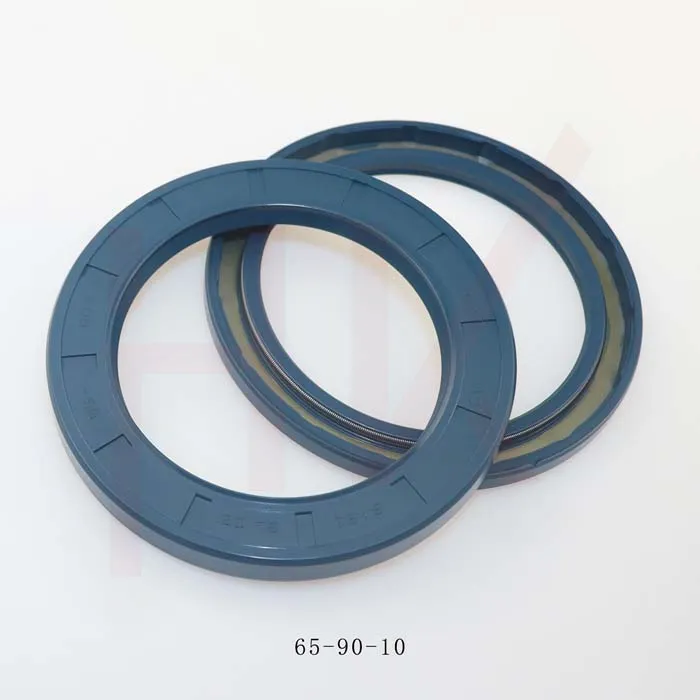
One of the most popular materials used in hydraulic cylinder seal kits is polyurethane. Known for its abrasion resistance and ability to withstand high pressures, polyurethane seals offer longevity and efficiency in dynamic applications. Their resilience against wear and tear, even under arduous conditions, makes them a preferred choice for heavy-duty industrial machinery and construction equipment. Furthermore, polyurethane’s flexibility allows it to adapt to pressure fluctuations, reducing the risk of leaks and enhancing operational efficiency.
Another widely used material is nitrile rubber, also known as Buna-N. This material is esteemed for its excellent resistance to oil and grease, making it ideal for environments where hydraulic fluids can degrade seals. Nitrile rubber's ability to retain its properties even at high temperatures contributes to its popularity in automotive and aerospace hydraulic systems. Its cost-effectiveness and mechanical strength make it an economical yet reliable choice for a variety of applications.
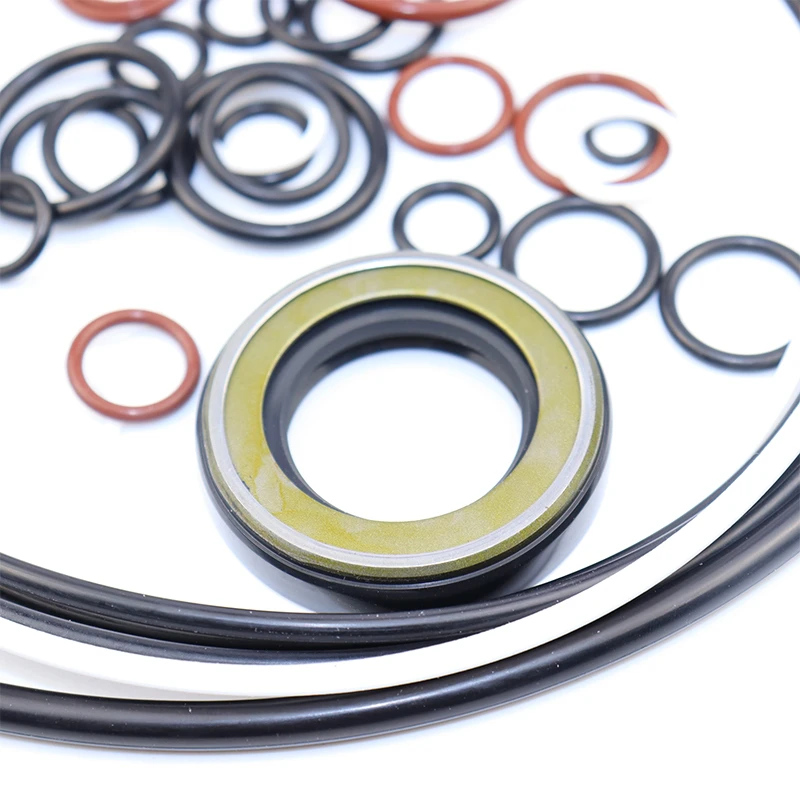
Viton, or fluoroelastomer, is favored in scenarios where extreme temperature and chemical resistance are critical. Withstanding temperatures ranging from -20°F to 400°F (-29°C to 204°C), Viton seals maintain their integrity in environments where other materials could falter. This makes them suitable for use in the chemical processing and oil and gas industries, where exposure to harsh chemicals is common.
hydraulic cylinder seal kit material
For applications where cleanliness and compliance to health standards are pivotal, FDA-approved silicone seals are typically used. These seals are employed in the food processing and pharmaceutical industries where their ability to resist microbial growth and withstand sterilization processes is indispensable. Silicone’s excellent flexibility and stability over a wide temperature range further enhance its suitability for such sensitive applications.
Engineering plastics such as PTFE (Polytetrafluoroethylene) are also prevalent in hydraulic seal kits, particularly in industries where low friction and chemical inertness are required. PTFE seals excel in minimizing frictional forces, thereby reducing wear and improving the efficiency of hydraulic systems. Their exceptional resistance to almost all chemicals makes them a go-to choice in environments where both mechanical and chemical robustness is needed.
The selection of the appropriate hydraulic cylinder seal kit material is not only technical but also strategic, impacting both performance and maintenance costs. Companies striving to optimize their hydraulic systems must carefully assess the working conditions, including temperature, pressure, and the presence of chemicals, to make informed decisions about seal kit materials. Additionally, engaging with experts in hydraulic systems can provide insights into the latest advancements and best practices in seal technology, ensuring that your hydraulic systems remain reliable and cost-effective.
Reliability and durability in hydraulic systems are non-negotiable, necessitating an authoritative understanding of seal kit materials and their interactions with hydraulic fluids and environmental conditions. Trust in your hydraulic system's performance is built on the bedrock of informed material choice, backed by technical expertise and credible experience in the field. As technology advances, staying current with material innovations and applying this knowledge to your hydraulic systems will ensure sustained operational excellence and cost efficiency.