Selecting the right material for a hydraulic cylinder seal kit is essential for ensuring optimal performance and longevity in various applications. As hydraulic systems operate under high pressure and varying temperatures, the choice of seal kit material plays a crucial role in maintaining the integrity and efficiency of the equipment. Here, we delve into the key aspects of hydraulic cylinder seal kit materials, providing insights drawn from real-world experience and professional expertise to guide you toward a trustworthy decision.
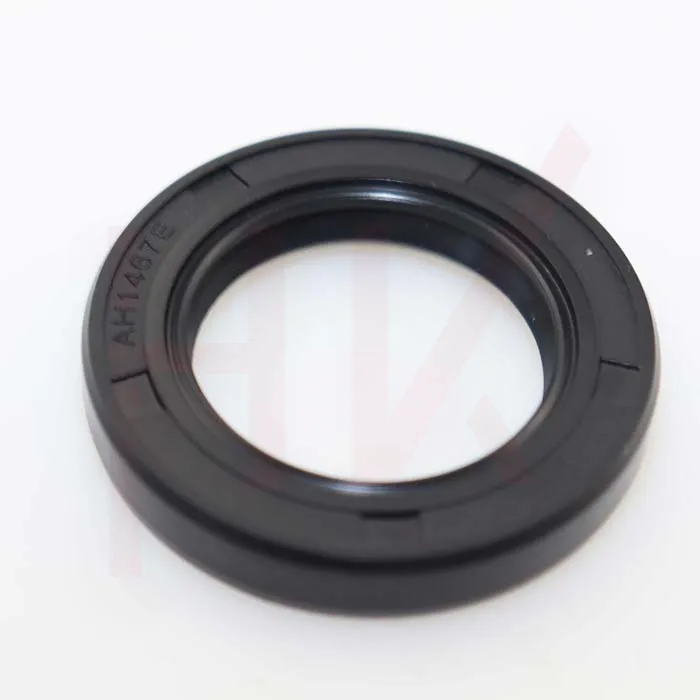
One of the primary considerations in selecting a seal kit material is understanding the specific requirements and operating conditions of your hydraulic system. For instance, systems exposed to extreme temperatures or aggressive chemicals necessitate materials with specific qualities. Nitrile Rubber (NBR) is commonly chosen for general purposes due to its excellent resistance to petroleum-based oils and hydraulic fluids. However, for applications involving higher temperatures or exposure to ozone and weathering, Ethylene Propylene Diene Monomer (EPDM) or Fluorocarbon (Viton) are preferred for their superior resistance characteristics.
Polyurethane is another material frequently used in hydraulic cylinder seal kits due to its remarkable abrasion resistance and load-bearing capacity. It is particularly effective in high-pressure applications but can degrade when exposed to water-based fluids or high temperatures. This underscores the importance of matching the material to the hydraulic fluid utilized in the system.

From a professional standpoint, it is essential to consider not just the operational environment, but also the compatibility of the seal kit materials with the metals used in the construction of hydraulic cylinders. Incompatible materials can lead to chemical reactions that degrade both the seals and the metallic components, leading to system failure. Polytetrafluoroethylene (PTFE), for example, is noted for its chemical inertness and can be used in tandem with almost any metal without adverse effects, making it an excellent choice for applications requiring both chemical resistance and low friction.
hydraulic cylinder seal kit material
Real-world experience teaches us that the longevity of hydraulic systems can be heavily influenced by how well the seals maintain their structural integrity and functionality over time. For industries relying heavily on hydraulic systems, such as construction or manufacturing, the financial and operational repercussions of unexpected downtimes can be significant. In such contexts, investing in high-quality seal kits with premium materials can lead to substantial cost savings and operational efficiency over time.
From an authoritative viewpoint, experts recommend conducting a thorough analysis of wear patterns and failure modes in hydraulic seals during routine maintenance checks. This data-driven approach enables you to select materials that not only meet immediate operational needs but also provide enhanced durability and reliability. Additionally, consulting with seal manufacturers or suppliers who possess a deep understanding of material science and engineering is advisable. These professionals can offer valuable insights into emerging materials and technologies that align with the latest developments in hydraulic systems engineering.
Trustworthiness in the selection of hydraulic cylinder seal kit materials is solidified by relying on suppliers and manufacturers that adhere to internationally recognized quality standards. Performance certifications and material data sheets provide transparency and confidence in the materials being utilized. Partnering with reputable brands that offer warranties and customer support further enhances reliability and minimizes risk.
In conclusion, the selection of hydraulic cylinder seal kit materials is a nuanced process that requires a blend of technical knowledge, practical experience, and a commitment to quality. By considering factors such as fluid compatibility, environmental conditions, material properties, and supplier reliability, you are equipped to make informed choices that ensure the efficiency, longevity, and reliability of your hydraulic systems. Such diligence not only safeguards your equipment but also establishes a foundation for sustainable operational success.