Hydraulic cylinder seal kits are essential components in the realm of hydraulic systems, ensuring efficient and leak-free operation across numerous industries. Their quality and compatibility can make a substantial difference in performance and longevity. Understanding the intricate details of these seal kits can greatly enhance one's ability to maintain and optimize hydraulic systems.
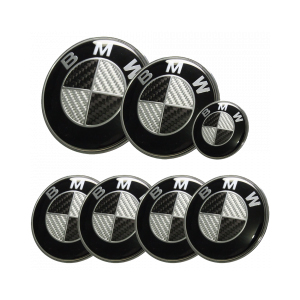
A hydraulic cylinder is a critical component that converts fluid power into mechanical force and motion, facilitating various industrial tasks such as lifting, pushing, pulling, and pressing.
These cylinders rely on precision-engineered components like seal kits to maintain their functionality. A hydraulic cylinder seal kit consists of various seals that prevent hydraulic fluids from leaking, thus maintaining optimal pressure within the system.
From my ample experience in the hydraulic industry, the selection of an appropriate seal kit is not just about matching dimensions; it’s rooted in understanding the environmental conditions and operational dynamics of the system. The quality of hydraulic cylinder seal kits can be gauged through various parameters such as material resilience, resistance to wear and tear, and flexibility to adapt to temperature changes.

The materials used in manufacturing these seal kits play a pivotal role in their performance. High-grade options often include nitrile rubber (NBR), Viton, and polyurethane. Each material presents different advantages; for example, NBR offers excellent resistance to abrasion and a broad temperature range, whereas Viton is particularly esteemed for its superior resistance to heat. Choosing the correct material requires an in-depth understanding of the system requirements and the specific environment in which it operates.
As an expert in hydraulic technologies, I have observed that the importance of maintaining seal integrity cannot be understated. A compromised seal kit can lead to significant leaks, resulting in a drop in system efficiency and potential equipment downtime. Regular inspections and timely replacements are essential. A damaged seal often exhibits visible signs like cracks, deformation, or brittleness. Addressing these issues promptly ensures the continuity and reliability of the hydraulic system.
hyd cylinder seal kit
Trustworthiness in seal kit suppliers is another facet that deserves special attention. Partnering with reputable manufacturers who adhere to international standards such as ISO can significantly mitigate risks associated with substandard products. It is always recommended to source seal kits from vendors with proven industry experience and a robust quality assurance process.
On the authority front, leveraging knowledge from technical guides and industry standards can empower stakeholders in making informed decisions. Many experienced technicians rely on resources such as manufacturer datasheets that provide comprehensive insights into seal compatibility, installation procedures, and maintenance tips. Additionally, forming a network with industry professionals and participating in forums can also provide valuable real-time advice and updates.
My expertise further highlights the role of technological advancements in enhancing seal kit durability. Modern manufacturing techniques, such as CNC machining and CAD design, allow for precision-engineered seals that perfectly accommodate the hydraulic cylinder dimensions, thus minimizing installation challenges. These advancements also facilitate customizable solutions to address unique operational needs, thereby broadening the scope of applications.
In conclusion, hydraulic cylinder seal kits are more than mere accessories; they are fundamental to the optimal operation of hydraulic systems. Knowledge of their materials, functionality, maintenance, and the importance of sourcing from credible suppliers underpins their successful application. With advancements in manufacturing and materials science, today's seal kits offer improved performance, underscoring their indispensable role in industrial and mechanical applications. Adapting to these innovations and grounding decisions in expertise and trust can assure the efficient, reliable operation of hydraulic systems, ultimately driving organizational success.