Imagine this a vibrant industrial facility where precision and efficiency reign supreme. The hum of machines and the rhythmic clattering of operating equipment form a symphony of production. Amidst this bustling scenario is a small yet indispensable component—hub rubber seals. While seemingly minor, the hub rubber seal's role is monumental, anchoring a spectrum of industries by ensuring optimal functionality and longevity.
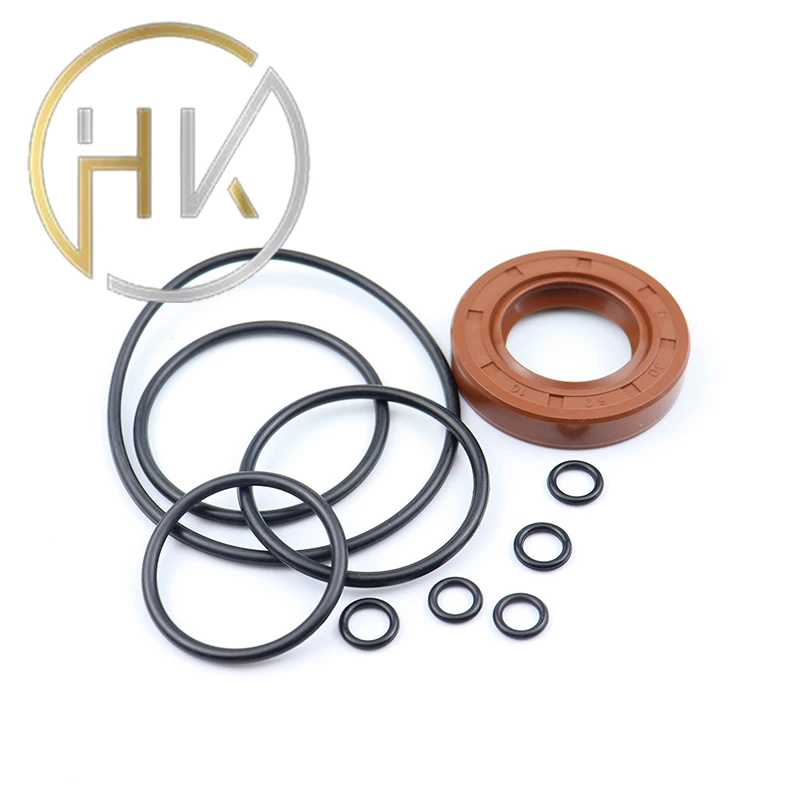
A common sight in automotive, aerospace, and manufacturing applications, the humble hub rubber seal offers a microcosm of technological advancement. Engineered to perfection, these seals work tirelessly to prevent leaks, block contaminants, and maintain the integrity of fluids, gases, or solid particulates. A failure in one of these inconspicuous components can lead to increased downtime, escalated maintenance costs, and, ultimately, compromised equipment efficiency.
From my years of deep-rooted experience within the field, it's evident that selecting the ideal hub rubber seal involves acute precision and understanding. One size does not fit all, and the choice of seal depends significantly on factors such as chemical compatibility, temperature range, and pressure limits. Silicone-based seals might thrive in the frigid expanses of arctic conditions, while Nitrile-based alternatives shine in the heat of an automotive engine.

Expertise in hub rubber seal technology does not merely involve material selection. The design nuances of these seals dictate their effectiveness. A lip seal design might be appropriate for one application, while a face seal design fits another. Such specialized knowledge empowers industries to tailor their seal choices to specific operational needs, reducing friction and wear over time, thus extending the service life of their machinery.
hub rubber seal
With authority comes the responsibility to advance industry standards, and hub rubber seals are no exception. The meticulous engineering that goes into these products is backed by rigorous testing to meet stringent standards. Manufacturers often subject these seals to accelerated aging processes, chemical exposure tests, and pressure cycling, striving to quantify their durability and performance. This relentless pursuit of excellence reflects in certificate endorsements from respected bodies, a testament to the authority and reliability embedded in every seal.
Trustworthiness is earned through consistent performance. It's the bedrock on which long-term industrial relationships are forged.
Hub rubber seals are no strangers to this principle. In environments where machine efficiency is paramount and downtime is costly, industries place their trust in these components to perform without fail. Routine reports and feedback loops are integral to this trust, providing data that informs enhancements and adjustments, thus perpetuating a cycle of improvement.
The ongoing evolution in hub rubber seal technology is a testament to innovation at its best. Research and development departments are constantly pushing boundaries—exploring new polymers, refining manufacturing processes, and implementing cutting-edge technologies like computer-aided design (CAD) and finite element analysis (FEA) to predict performance issues before they even occur.
In conclusion, the narrative of hub rubber seals is a compelling tale of silent guardianship. Through precision engineering, expert knowledge, authoritative testing, and unwavering reliability, these seals play an essential yet often overlooked role in the machinery that drives modern life. As industries continue to advance and expand, the value of choosing the right hub rubber seal cannot be overstated, for it is these small yet potent components that keep the wheels of progress turning smoothly. Their legacy is built on trust, fortified by expertise, and recognized through consistent performance, forging pathways to future innovations and increased industrial reliability.