High pressure shaft seals are essential components in various industrial applications, tasked with preventing leakage, contamination, and managing pressure differentials between the inside and outside of rotating equipment. These robust seals play a crucial role in maintaining the efficiency and longevity of machinery such as turbines, compressors, and pumps, all of which are foundational to many sectors including oil and gas, power generation, and chemical processing.
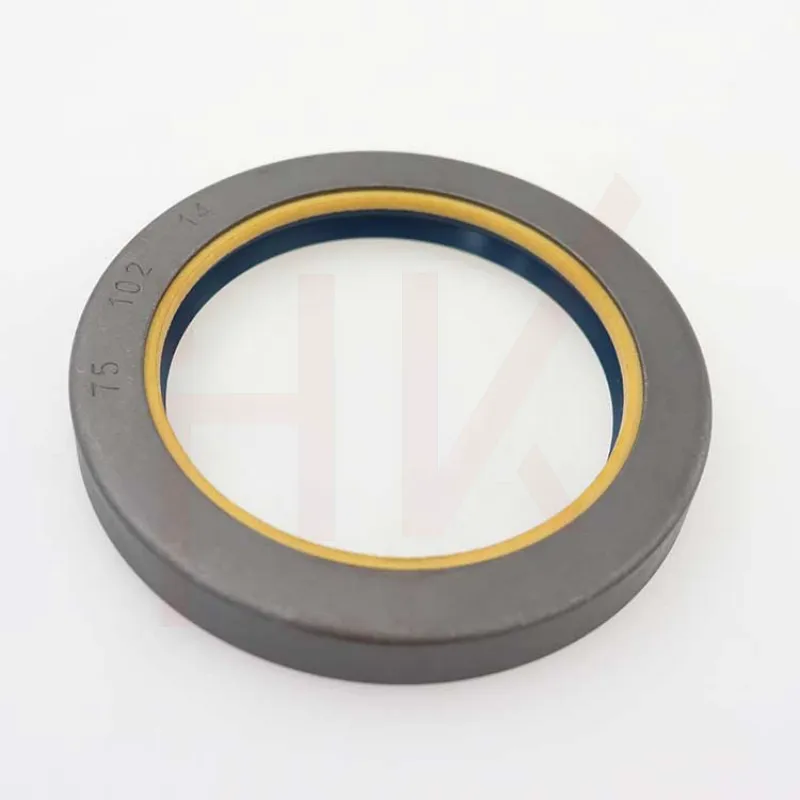
A significant area of focus when examining high pressure shaft seals is their design and material composition. These seals are often designed using advanced materials that can withstand extreme pressures and temperatures, while simultaneously providing reliable sealing capabilities. Materials such as fluoroelastomers and polytetrafluoroethylene (PTFE), known for their resilience against chemical and thermal stress, are frequently used to ensure durability and performance. Furthermore, the integration of metallic components helps in accommodating various expansion coefficients, thus providing additional structural integrity under high pressure conditions.
The innovation in seal design has advanced significantly, with manufacturers increasingly relying on computer-aided design (CAD) and finite element analysis (FEA) to predict performance under different operational scenarios. This ensures that the seals are not only tailored to specific applications but are also reliable in unforeseen conditions. These technologies enable engineers to optimize seal geometry and material distribution, enhancing their effectiveness and lifespan.
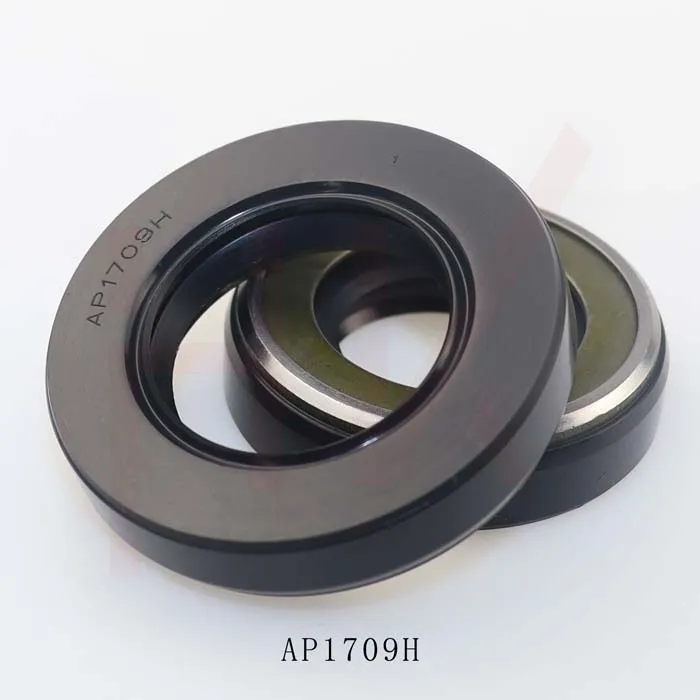
Expertise in selecting the appropriate shaft seal is vital, as the wrong choice could lead to equipment failure, costly repairs, and downtime. Professionals in the field meticulously analyze operational parameters such as pressure levels, temperature ranges, rotational speed, and the nature of the fluid being sealed. This data-driven approach ensures that the selected seal not only meets the immediate requirements but also adheres to safety and regulatory standards. The deployment of high-quality seals crafted by experienced manufacturers who comply with international quality standards such as ISO 9001 offers companies reassurance regarding performance and safety.
high pressure shaft seals
Maintaining Authoritativeness in the arena of high pressure shaft seals involves continuous research and development. Collaborations with academic institutions and participation in industry forums are two ways in which manufacturers and key industry players further their understanding of emerging materials and technologies. By staying informed of the latest advancements and sharing knowledge, these entities strengthen their position as thought leaders whose products are at the forefront of technological evolution.
Trustworthiness is another pillar vital to the reputation of high pressure shaft seal providers. The ability to deliver consistent quality, provide bespoke solutions, and maintain transparent communication with clients establishes trust in the marketplace. Additionally, the provision of extensive after-sales support, training, and warranty services reassures clients regarding their investment. By showcasing case studies, testimonials, and independent performance evaluations, companies can further bolster their credibility and showcase their commitment to customer satisfaction.
In conclusion, high pressure shaft seals are indispensable across multiple industries, where their role is to sustain equipment reliability and efficiency under demanding conditions. Mastery over their design, selection, and maintenance directly impacts machinery operation and the wider industrial processes they support. As technology evolves, the continued emphasis on experience, expertise, authoritativeness, and trustworthiness will ensure that high pressure shaft seals remain effective and relevant, driving industrial progress and innovation.