High-pressure rotary shaft seals play a pivotal role in the reliability and performance of a wide array of industrial applications. Whether it’s safeguarding the integrity of a complex hydraulic system or ensuring the seamless operation of high-speed machinery, these components are indispensable. Understanding their intricacies not only assists in selecting the right seal but also ensures optimum efficiency and safety in operations.
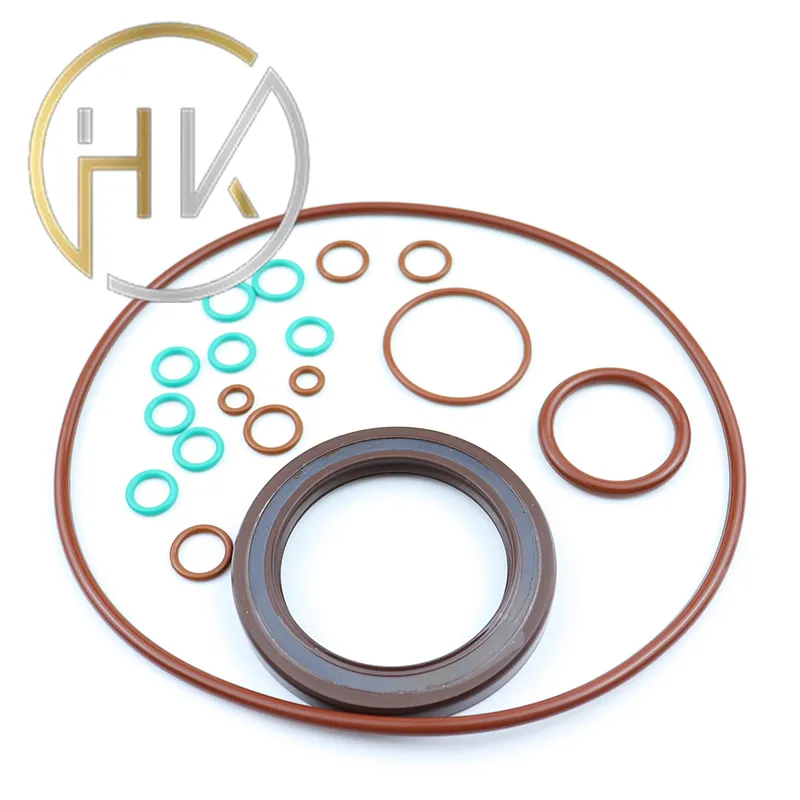
Rotary shaft seals, also known as lip seals or oil seals, are engineered to retain lubricants and block contaminants. However, in high-pressure environments, standard seals may falter, leading to leaks, equipment damage, or catastrophic failures. Therefore,
choosing the right high-pressure rotary shaft seal is paramount.
The versatility of these seals lies in their ability to withstand pressures exceeding the standard operating conditions. These specialized seals are constructed using advanced materials, such as reinforced elastomers and thermoplastics, which offer superior resistance against degradation from temperature fluctuations, aggressive chemicals, and mechanical stresses. Fluorocarbon (FKM) and polytetrafluoroethylene (PTFE) are popular choices due to their exceptional durability.
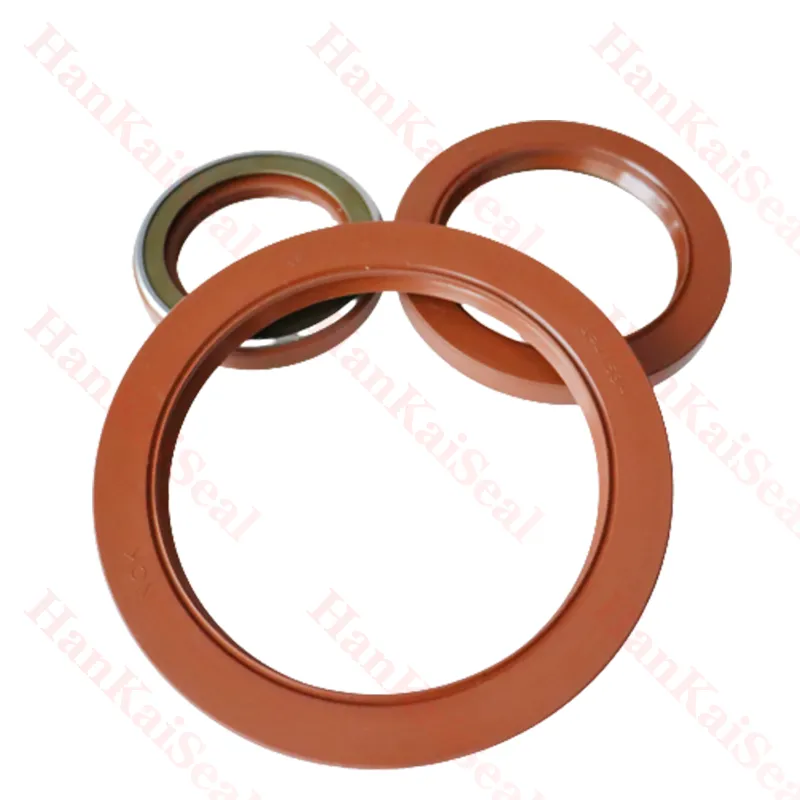
In high-pressure systems, common issues such as extrusion, deformation, and friction-induced wear are exacerbated. Thus, the design considerations for these seals invariably focus on balancing flexibility with rigidity. This often involves multi-component structures featuring support rings or backup rings made of rigid plastics or metals, serving to counteract extrusion and maintain a reliable seal under pressure.
The success of high-pressure rotary shaft seals also hinges on their lip design. Single-lip seals facilitate simplicity and are ideal for lower pressure applications. In contrast, multi-lip configurations or those incorporating secondary sealing elements are preferable in demanding environments. These designs provide enhanced protection against leaks while accommodating misalignments and shaft runouts.
Field experience underscores that selecting the right seal size is as critical as the design. An ill-fitting seal can lead to premature wear or immediate failure. Users are advised to meticulously measure the shaft diameter, bore size, and seal width. The seal specifications should align with these measurements, taking account of expansion or contraction due to thermal conditions.
high pressure rotary shaft seals
The installation of high-pressure rotary shaft seals demands a careful approach. During installations, any damage to the seal surface can compromise functionality. It is essential that the seating surfaces are spotless and free of nicks or scratches. Installing tools such as tapered sleeves or bullet tools can facilitate smooth installation, minimizing the risk of damaging the primary lip or secondary components.
Moreover, regular maintenance of these seals significantly extends their lifespan. Routine inspection is crucial, assessing for signs of wear, such as hardening, cracking, or excessive lip wear. Lubrication is another critical element; using incompatible or inadequate lubricants can result in increased friction, leading to seal failure. It is advisable to adhere to manufacturer recommendations regarding both the type and volume of lubricant to be applied.
The impact of technological advancements cannot be overstated in the realm of high-pressure rotary shaft seals. Innovations in materials science continue to push the boundaries of what these seals can achieve, ensuring they remain at the forefront of machinery reliability. As industries demand higher efficiencies and operational safety, the developments in seal technology provide an essential component to achieving these goals.
The expertise involved in the engineering and application of these seals imparts a level of authority and trustworthiness essential for industrial leaders. Collaboration with experienced manufacturers or consulting with seal experts can provide valuable insights, ensuring the correct specification and installation. They bring a comprehensive understanding of material properties, loading conditions, and fluid dynamics that is vital for the optimal operation of high-pressure systems.
In conclusion, high-pressure rotary shaft seals are more than just machine components; they are keystones in industrial operations that demand reliability and exceptional performance. By leveraging the right materials, designs, and installation practices, industries can achieve unparalleled efficiency and operational security. For those in charge of maintaining industrial equipment under extreme conditions, understanding these seals is not just beneficial—it is pivotal to success.