High pressure rotary shaft seals are integral components in many industrial applications, often serving as the unsung heroes that ensure the smooth operation and longevity of complex machinery. Preventing leakage and contamination is their primary task, making them indispensable in sectors such as automotive, aerospace, and manufacturing. Drawing on years of industry experience and professional expertise, this article delves into the nuances of high pressure rotary shaft seals, focusing on their design, functionality, and the critical factors that contribute to their effectiveness.
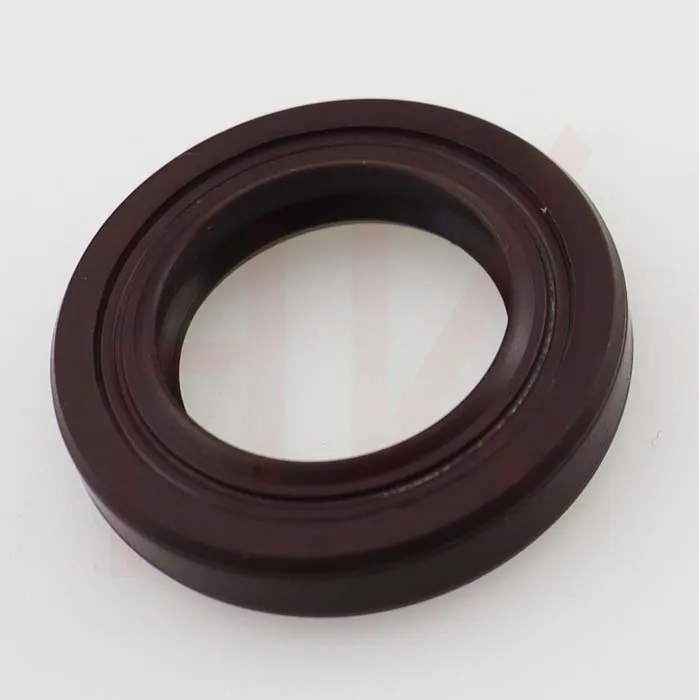
The architecture of high pressure rotary shaft seals is specifically engineered to manage the demands of modern industrial machinery. These seals must withstand significant pressure differentials while maintaining their sealing integrity. The sophisticated design typically involves multiple components, including the primary sealing lip, secondary sealing lip, metal casing, and the spring element. The primary sealing lip is often made from advanced elastomeric materials that can endure high temperatures and pressures. The secondary lip serves as a protection barrier against external contaminants such as dust and moisture, enhancing the seal's longevity.
The selection of material for these seals is a finely-tuned process that balances durability, flexibility, and chemical resistance. Fluoroelastomers, PTFE, and other synthetic rubbers are frequently chosen for their remarkable ability to withstand the rigors of high-pressure environments. Material expertise is crucial, as using the incorrect material can lead to premature failure, costly downtimes, or catastrophic equipment damage. Proper material selection is a testament to a supplier’s expertise and authority in the field.
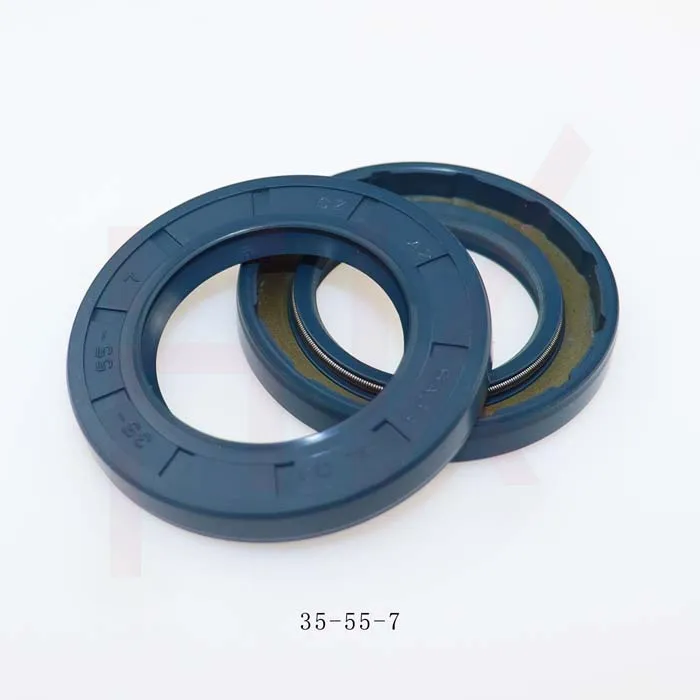
A pivotal element in assessing the effectiveness of rotary shaft seals lies in their design precision and manufacturing accuracy. Precision engineering ensures that seals maintain their performance thresholds under high dynamic conditions. Tolerances in seal design are kept minimal to ensure an exact fit and high performance. This level of precision requires authoritative knowledge of both the machinery the seals will be used in and the environments they will be exposed to.
high pressure rotary shaft seals
In terms of deployment, the success of these seals is heavily reliant on correct installation and maintenance. Trustworthiness is showcased by manufacturers who provide detailed installation guides, offering thorough insights into seating the seal correctly to prevent misalignment or damage. Furthermore, regular maintenance check-ups, backed by empirical data and performance charts, help predict seal lifecycles, thus avoiding unexpected failures and costly repairs.
From an authority and expertise perspective,
selecting the right high pressure rotary shaft seal supplier is crucial. Manufacturers distinguished by robust research and development capabilities tend to offer innovative sealing solutions that not only fit the technical requirements but also push the envelope in terms of durability and performance. These suppliers bring an authoritative voice to the table, offering consultations based on real-world data and case studies that highlight their commitment to quality and excellence.
The field of rotary shaft seals continues to evolve with technological advancements. For instance, smart seals with embedded sensors for proactive condition monitoring are on the rise. This technology serves to provide real-time feedback on seal integrity and operation conditions, significantly boosting reliability and trustworthiness. As a testament to professional expertise, leading companies are at the forefront of integrating such innovations, reinforcing their authoritative status in the industry and paving the way for smarter, more efficient machinery.
In conclusion, high pressure rotary shaft seals are critical components that require a blend of experience, expertise, and authoritative design to ensure trust in their application. As industrial needs grow more complex and demanding, so too does the need for high-quality, reliable sealing solutions. By choosing the right materials, maintaining precision engineering standards, and embracing innovative technologies, businesses can significantly enhance the operational reliability and longevity of their machinery, ensuring smooth and efficient operations.