Excavator cylinder seal kits are vital components for ensuring the longevity and efficiency of hydraulic systems in heavy machinery. These seal kits play a significant role in preventing fluid leakage and contamination, which can lead to costly downtimes and equipment inefficiencies. Understanding their importance and how to select and maintain these kits can make a substantial difference in the performance of your excavator.
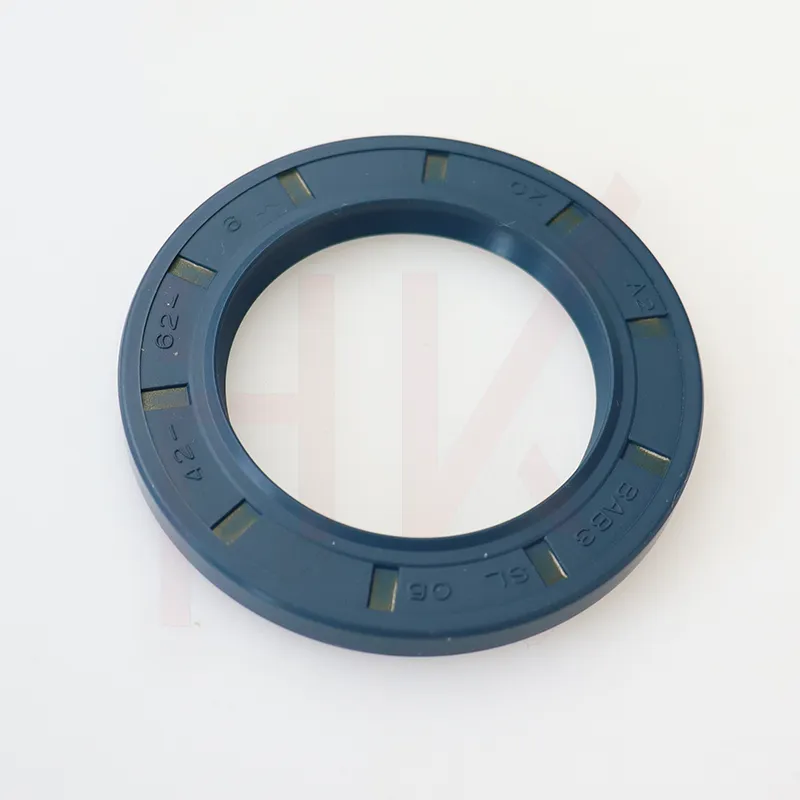
Choosing the right excavator cylinder seal kit requires both technical expertise and practical experience. With an array of options available on the market, each designed to meet specific requirements, the selection process can be daunting for anyone without specialized knowledge. Professionals in the heavy machinery field, who regularly work with hydraulic systems, know the value of selecting high-quality seal kits. These kits are specifically engineered to withstand extreme pressures and temperatures, thus ensuring the optimal functionality of the hydraulic cylinders.
When selecting a seal kit, one must consider the type of excavator and its specific operational requirements. For instance, the type of hydraulic fluids used, the operating environment, and the load capacity can all influence the kind of seals needed. A seal made of nitrile rubber might be suitable for certain conditions, whereas polyurethane or PTFE might be better for others. From a professional standpoint, keeping an inventory of different types of seals is ideal for ensuring quick replacements and minimal machine downtime.
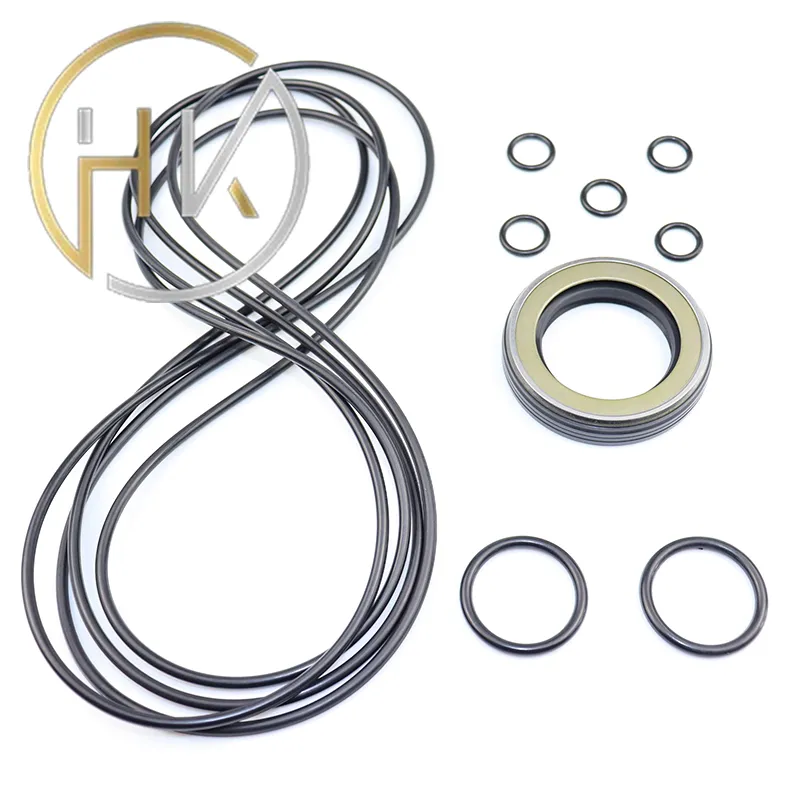
Real-world experience has shown that neglecting the maintenance of seal kits can lead to significant operational issues. The common signs that a seal kit needs attention include sluggish machine movement, visible fluid leaks, or a noticeable loss in hydraulic pressure.
Regular inspections of the excavator cylinder seals are recommended. During these inspections, it’s essential to look for any signs of wear and tear, such as cracks or deformations in the seals, which can compromise the system's integrity.
excavator cylinder seal kits
The expertise in handling excavator cylinder seal kits is not just in their selection but also in their installation. Incorrectly fitted seals, or using the wrong type of sealant, can exacerbate leakage problems instead of fixing them. That's why it is paramount for heavy machinery operators to engage trained technicians for seal replacements and repairs. These technicians bring both theoretical knowledge and hands-on experience to ensure that the job is done correctly, preserving the equipment's functionality and performance.
Authoritativeness in the use of excavator cylinder seal kits comes from sourcing these components from reputable manufacturers. Companies with a proven track record in the production and supply of high-quality seal kits often undergo rigorous quality assurance processes, which instills confidence in the end-user. Top manufacturers will provide not only a superior product but also support services, detailed installation guides, and technical support, which are invaluable resources for machinery owners and operators.
When it comes to trustworthiness, it's essential to align with a supplier that offers transparency in their product specifications and sourcing practices. A credible supplier will be open about the materials used, the testing procedures employed, and the warranties provided. They understand that trust is built on consistent quality and service. This reliable partnership ensures that machinery owners have immediate access to replacement parts, thereby reducing the risk of extended downtime.
In conclusion, the selection, maintenance, and sourcing of excavator cylinder seal kits are critical factors that affect the performance and safety of heavy machinery. Leveraging the combined strength of experience, expertise, authoritativeness, and trustworthiness can drastically enhance operational efficiency. For machine operators and owners, investing the time to understand and properly manage these components pays dividends in machine reliability and longevity. By following best practices and consulting with industry professionals, users can ensure their hydraulic systems remain robust and efficient, ultimately securing a return on their investment through reduced maintenance costs and enhanced productivity.