When considering seals for mechanical systems, the distinction between dust seals and oil seals is crucial for optimal performance and longevity. Understanding their specific roles and applications can significantly impact equipment efficiency and maintenance requirements.

Dust seals are primarily designed to prevent contaminants such as dust, dirt, and other environmental particles from entering mechanical assemblies. These seals are typically found in applications where external environments pose significant threats to the integrity of machinery, like construction equipment or vehicles operating in harsh terrains.
Materials like rubber and Teflon are often employed in dust seal construction, offering flexibility and resilience under varied conditions. The seal's simplicity lies in its design, aimed at offering a protective barrier without the need for intricate structures that engage with environmental elements.
On the other hand, oil seals (also known as shaft seals, radial lip seals, or rotary seals) serve a dual function they retain lubricants within a system while simultaneously preventing contaminants from compromising the lubrication. The presence of oil seals is critical in automotive engines, gearboxes, and any rotating shafts where the lubrication must be maintained to ensure smooth and efficient operation. They are typically made from materials such as nitrile rubber, silicone, or fluoroelastomer, which are chosen to withstand various temperatures and chemical exposures. This dual role demands a more complex structure, often involving metal cases for rigidity and a flexible sealing lip that maintains pressure and reduces friction on the shaft.
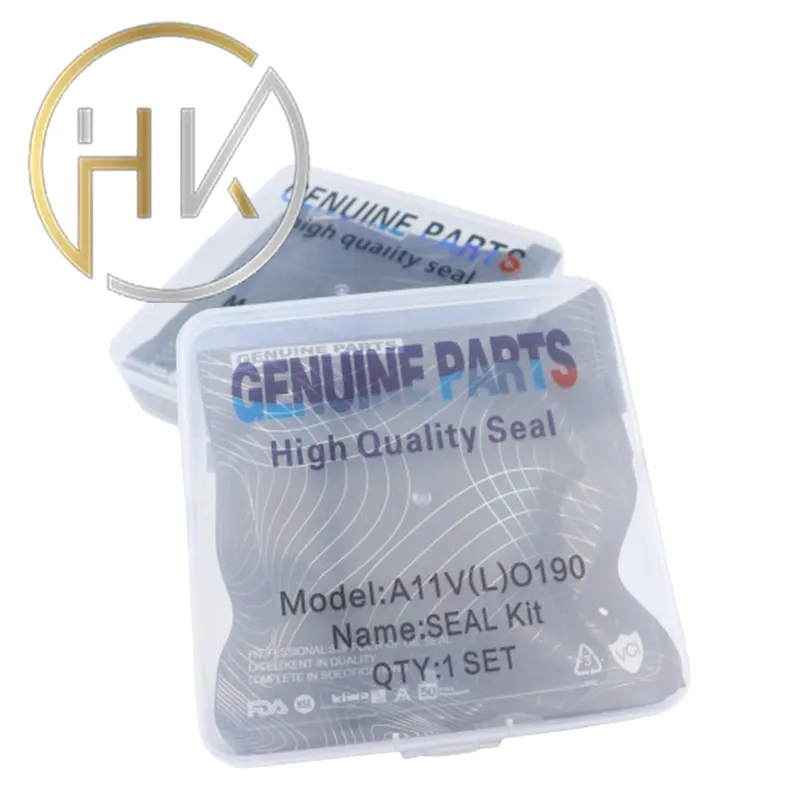
Both seal types are imperative in high-performance applications, but their specific mechanisms cater to distinct operational challenges. Dust seals are ideally suited for static conditions, where the seal does not need to accommodate moving components but must simply block external elements. Conversely, oil seals are critical in dynamic applications where moving parts require constant lubrication to mitigate friction. This distinction highlights the importance of selecting the right seal for the job; failure to do so can lead to increased wear and tear, equipment malfunction, or even catastrophic failures.
dust seal vs oil seal
In practice, the choice between dust seals and oil seals involves assessing the operational environment the presence of contaminants, the need for lubrication, and the type of motion involved. For instance, industrial or agricultural machinery that faces significant dust exposure alongside rotary components might benefit from a combination of both seal types, utilizing dust seals for static interfaces and oil seals on rotating shafts.
A common misconception is that one type of seal can replace the other, but the roles they play are distinct and non-interchangeable. Attempting to use an oil seal for dust exclusion alone might lead to unnecessary friction and wear, while relying on a dust seal for oil retention can result in lubricant leakage and system failure.
Maintenance and inspection routines should also reflect the specific needs of each seal type. Dust seals require periodic checks for wear, cracks, or material hardening that could compromise their ability to exclude contaminants. Oil seals, in contrast, need inspection for oil weepage or leaks, and checking the condition of the sealing lip and spring (if present) for integrity loss due to friction.
Selecting and maintaining the appropriate seal improves system reliability, ensuring machinery functions efficiently and remains protected against environmental aggressors. Understanding the differences and employing the right seal type based on their specific applications not only enhances machine performance but also extends the lifespan of vital components. In conclusion, recognizing when to deploy dust seals versus oil seals is a key factor in mechanical design and maintenance strategies, driving longer service life and reduced downtime for industrial equipment.