When it comes to maximizing the performance and longevity of hydraulic and pneumatic systems, one component frequently stands out the cylinder wiper seal. As a vital part of such machinery, the wiper seal directly impacts system efficiency by preventing contaminants from entering the cylinder and causing wear or damage. This article explores the nuanced role of cylinder wiper seals, shedding light on why choosing the right seal is crucial for optimal system performance.

Cylinder wiper seals, sometimes referred to as scrapers or excluders, serve the fundamental purpose of scraping away dirt, dust, and moisture from the piston rods as they retract into the hydraulic or pneumatic cylinder. Their presence is vital in ensuring contaminants do not breach the seal area, as foreign materials can lead to abrasion, scoring, and potentially catastrophic system failures.
In industrial settings,
the expertise of selecting the right wiper seal is imperative. The specifications of a wiper seal can vary greatly depending on the application requirements. From simple dust excluders made of thermoplastic materials to more complex dual-lip designs that offer additional exclusion capabilities, selecting a seal that aligns with the operating conditions is essential.
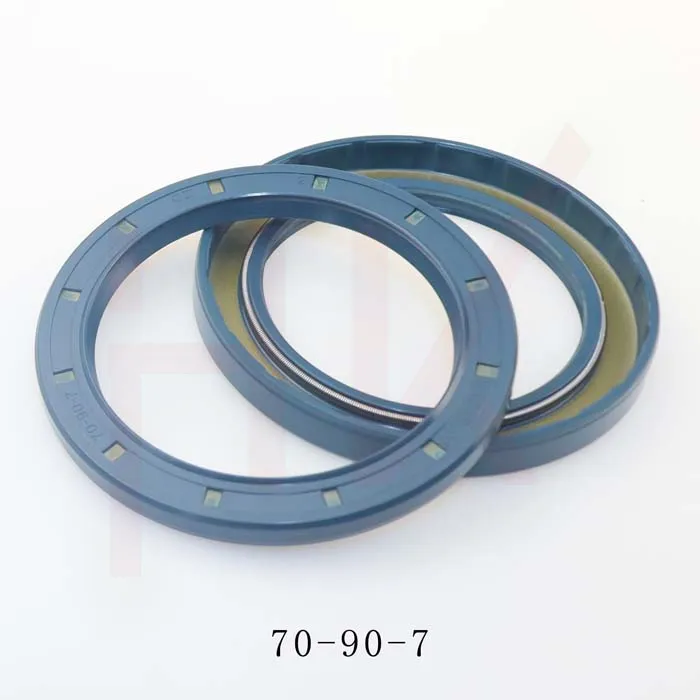
Material selection is a pivot of expertise when choosing a cylinder wiper seal. Among the various materials available—such as nitrile rubber, polyurethane, and PTFE—each provides distinct advantages and constraints. For example, polyurethane offers good wear resistance and resilience to tearing while working efficiently in temperatures ranging between -30°C and 80°C. Conversely, for environments that deal with higher temperatures and chemical exposure, PTFE becomes an ideal choice due to its outstanding chemical resistance and ability to perform at temperatures as high as 200°C.
In terms of authoritativeness, the importance of adhering to industry standards cannot be overstated. For instance, ISO 11943 outlines the international standards for contaminants control, which can directly affect the selection of the right wiper seal. Compliance with such standards not only ensures product reliability but also reinforces the credibility of the systems in which these seals are installed.
cylinder wiper seal
Trustworthiness in the selection and application of cylinder wiper seals also depends heavily on the manufacturer. It is advisable to source seals from reputable manufacturers who offer certifications and have a proven track record for their products in similar applications. Additionally, thorough testing—including dynamic testing simulating real-world operational conditions—can be advantageous in guaranteeing the trustworthiness of the wiper seals used.
Real-world experiences underline that poor seal performance can lead to costly downtime and repairs. For instance, in construction machinery where exposure to harsh, abrasive environments is common, a sub-par wiper seal can accelerate wear and result in leaks. Users have found that investing slightly more in high-quality seals can preemptively save on operational costs and downtime over the lifespan of machinery.
Finally, while cost considerations remain a significant factor in the decision-making process, it is the combination of consistent performance, reliability, and adherence to standards that should drive the choice of a cylinder wiper seal. It's about achieving a balance between cost and value, ensuring that the seals deliver long-term performance without compromising on quality or safety.
In conclusion, cylinder wiper seals may seem like a minor component in complex hydraulic and pneumatic systems, but their role is anything but trivial. They sit at the intersection of expertise, reliability, and safeguarding the integrity of entire systems. By making informed selections based on material properties, environmental conditions, and manufacturer credentials, businesses can enhance their operational efficiencies and extend the life of their equipment significantly.