Cylinder oil seals play a crucial role in maintaining the efficiency and longevity of hydraulic and pneumatic systems. These seals prevent leakage of fluids, ensuring that the internal components of machinery operate smoothly and effectively. The importance of choosing the right cylinder oil seal cannot be overstated, as it directly impacts the performance of equipment across various industries, including automotive, aerospace, and manufacturing.

Understanding the Material Composition
The primary composition of cylinder oil seals is typically rubber, silicone, or polytetrafluoroethylene (PTFE). Each material offers distinct advantages. For instance, rubber seals offer excellent elasticity and resistance to wear and tear, making them ideal for dynamic applications. Silicone seals are noted for their flexibility and ability to perform in extreme temperatures, while PTFE seals boast exceptional chemical resistance and low friction.
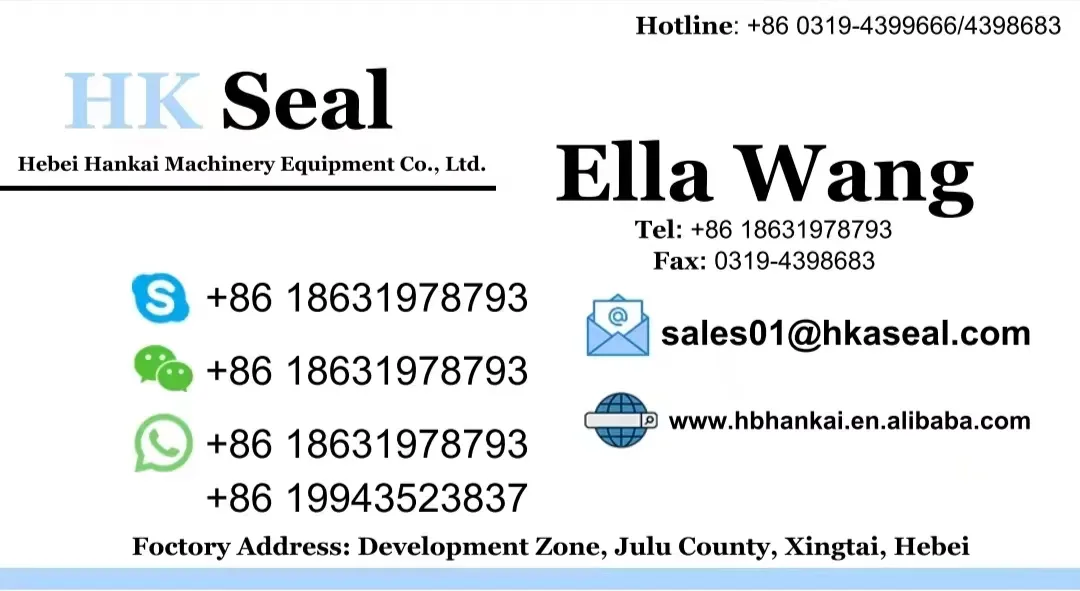
It is essential to select the material based on the specific operational conditions, including temperature range, pressure levels, and the type of fluid being used. The compatibility of the seal material with these factors enhances the overall performance of the cylinder, minimizing the risk of leaks and system failures.
Proper Installation Techniques
A professional approach to installing cylinder oil seals ensures optimal functionality and a longer lifespan. This involves correctly sizing the seal to fit the cylinder, ensuring a snug fit without excessive tightness that might lead to deformation or premature wear. Moreover, proper installation eliminates the chances of misalignment, which can cause uneven pressure distribution and eventual failure of the seal.
Lubrication during installation also plays a critical role. Using a compatible lubricant helps reduce friction during the initial operation, allowing the seal to adapt to its environment without undue stress. This step not only facilitates easier installation but also promotes the longevity of the seal.
Regular Maintenance and Inspection
cylinder oil seal
Regular maintenance and inspection are pivotal in preserving the integrity of cylinder oil seals. Routine checks can identify early signs of wear, such as cracking, hardening, or loss of elasticity. By addressing these issues promptly, one can avoid costly system breakdowns and maintain the overall efficiency of hydraulic systems.
Additionally, systematic cleaning of the equipment in which the seals are used can prevent contaminants from affecting the seal material. However, it’s critical to use appropriate cleaning agents that do not degrade the seal's composition, ensuring sustained performance.
Performance Optimization Strategies
Optimizing the performance of cylinder oil seals involves a strategic approach to both their selection and implementation. Customization of seals to meet specific system requirements can lead to enhanced precision and efficiency. This might include selecting surface finishes that reduce friction losses and enhance sealing capabilities under varying operational conditions.
Furthermore, implementing advanced monitoring technologies can provide real-time feedback on the condition of seals, allowing for predictive maintenance strategies. By leveraging such technologies, manual inspection intervals can be reduced, minimizing downtime and maintaining operational efficiency.
Application in Diverse Industries
Cylinder oil seals are integral to a variety of industries, each with unique demands. In the automotive sector, these seals contribute to the safe and efficient operation of braking and transmission systems, whereas in the aerospace industry, they ensure the reliability of hydraulic actuators under extreme pressures. The specificity of applications necessitates a nuanced understanding of seal selection and care, tailored to the unique requirements of each sector.
In conclusion, the effective use and maintenance of cylinder oil seals are paramount to the seamless operation of fluid control systems. Emphasizing material composition, precise installation, and regular maintenance can lead to significant improvements in system performance and longevity. As an expert in this field, ensuring an authoritative and trustworthy approach to seal management will translate to superior operational outcomes and sustained industrial productivity.