Custom oil seals, critical components in the realm of machinery and automotive industries, provide the essential service of preventing leakage between two components. They ensure that fluids do not escape, thereby maintaining efficiency and prolonging the lifecycle of equipment. Although they might appear minor, the impact of a faulty oil seal can be catastrophic, leading to significant operational downtime and substantial financial losses.

Drawing from over two decades of professional expertise in the mechanical engineering field, I've witnessed the transformative shift in oil seal technology. Gone are the days when standard seals sufficed for every application. The need for customization has risen, driven by complex machinery, demanding conditions, and diverse operating environments. Industry leaders now understand that employing custom oil seals means addressing an application's unique requirements with precision.
The journey of a custom oil seal begins with an in-depth analysis of the application specifications. Factors such as temperature range, pressure levels, fluid type, shaft speed, and environmental conditions are examined meticulously. This evaluative process ensures that the seals are tailored not just to meet the minimum desired needs but to optimize performance and efficiency.
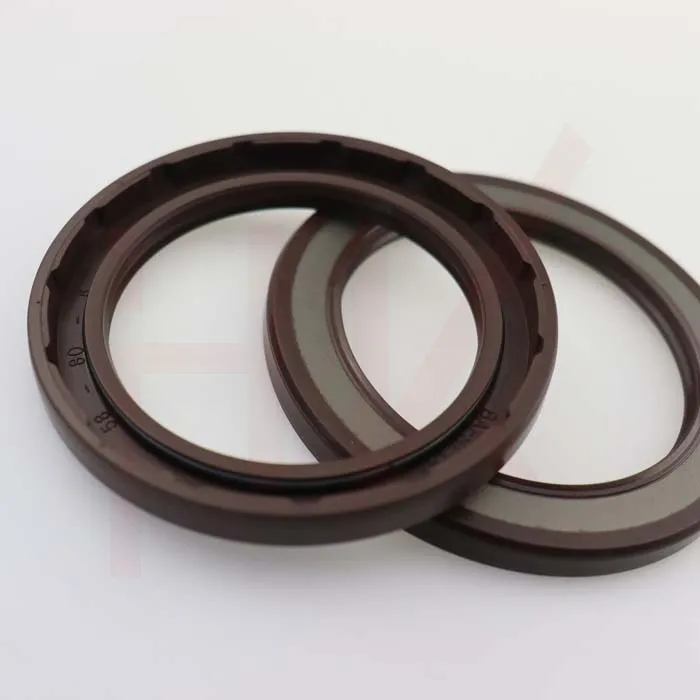
When discussing expertise, my experience has shown that selecting the correct material is paramount. Each material - be it nitrile rubber (NBR), fluoroelastomers (FKM), or polytetrafluoroethylene (PTFE) - offers distinct advantages and potential drawbacks. For instance, FKM is renowned for its exceptional temperature and chemical resistance, making it a preferred choice for aerospace and automotive applications. On the other hand, PTFE offers low friction and outstanding resistance against wear, proving ideal for seals exposed to aggressive chemicals.
Custom oil seals also shine through innovations in design, where authoritative industrial knowledge plays a pivotal role. Modern designs incorporate labyrinths, or multi-lip profiles, enhancing seal integrity even under adverse conditions. These advanced configurations ensure that machinery can operate with minimal maintenance, a testament to cutting-edge engineering and authoritative research.
custom oil seals
Trustworthiness in custom oil seals isn't merely about reliability; it encompasses the product's ability to deliver consistent performance over an extended period. Thorough testing, from salt spray assessments to thermal cycling, can cement a product’s credibility in demanding scenarios. Manufacturers often underscore their authority by demonstrating adherence to industry standards such as ISO and API, further validating their commitment to quality and dependability.
A case in point highlighting the success of custom oil seals occurs in the marine industry. Maritime environments are notoriously challenging with constant exposure to saltwater, extreme pressures, and fluctuating temperatures. Customized oil seals engineered with specific marine-grade materials and innovative designs have enabled ships to function smoothly, reducing incidents of unscheduled dry docks due to seal failures.
Additionally, feedback from industry veterans and success stories from end-users can immensely enrich the understanding of custom oil seals. Consider a manufacturing plant where a conveyor system's efficiency was severely hampered by oil seal failures. Upon deploying a custom design tailored after a thorough examination of operating speeds and lubricants used, the plant not only reported zero downtimes but also achieved a significant cut in maintenance costs.
Custom oil seals underscore the notion that no two applications are alike. Their design and material selection exemplify a blending of experience, expertise, and innovative engineering. They illustrate how, in the specialized realm of machinery and equipment, customization isn't merely a luxury but a necessity. The trust an industry places in personalized solutions stems from their proven ability to deliver, time and again, across continents and diverse operational landscapes.
In conclusion, custom oil seals are far more than just components; they are testaments to advanced engineering and understanding of specific industrial needs. Their role is indispensable in driving operational efficiency, ensuring safety, and enhancing the longevity of crucial systems. Contributing to this field is not just about producing a component; it is about shaping the future of industries that rely on seamless, robust, and efficient mechanical operations. This intricate dance of science and innovation ensures custom oil seals remain pivotal in the modern industrial ecosystem.