Custom oil seals play an integral role in the efficient operation of a wide range of machinery and equipment. As intricate as they seem, these components are designed to protect bearings and other moving parts from contamination and to retain lubricants within a system. Their significance cannot be overstated, making them a centerpiece for industries requiring precision and reliability.
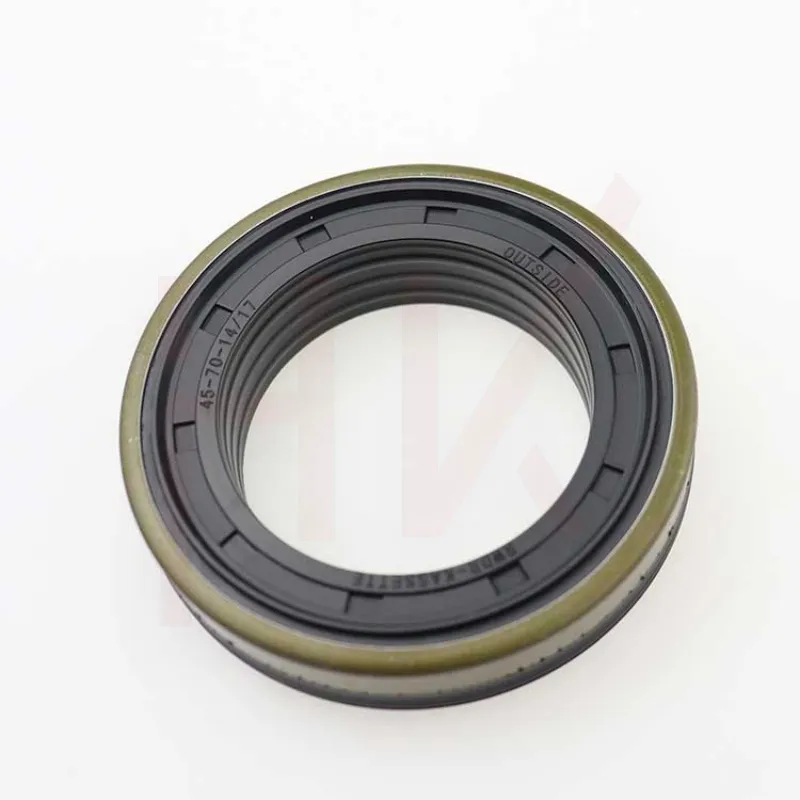
The experience of using custom oil seals varies significantly from standard off-the-shelf products. When designed specifically for a particular application, these seals offer an unmatched level of fit and function. One notable advantage is their ability to accommodate non-standard dimensions resulting from unique design requirements. For instance, machinery that confronts extreme environments or unconventional configurations relies heavily on custom oil seals to ensure optimal performance.
On the expertise front, creating custom oil seals demands a comprehensive understanding of material science and engineering. Not all seals are created equal; the choice of material directly influences their effectiveness and durability. Materials used in oil seals, such as nitrile, silicone, fluoroelastomer, and polyacrylate, each offer distinct properties. Selecting the right material involves assessing factors like temperature ranges, exposure to chemicals, and the levels of mechanical stress involved. Such expertise enables manufacturers to provide solutions that not only meet the specifications but enhance the lifespan of the machinery.
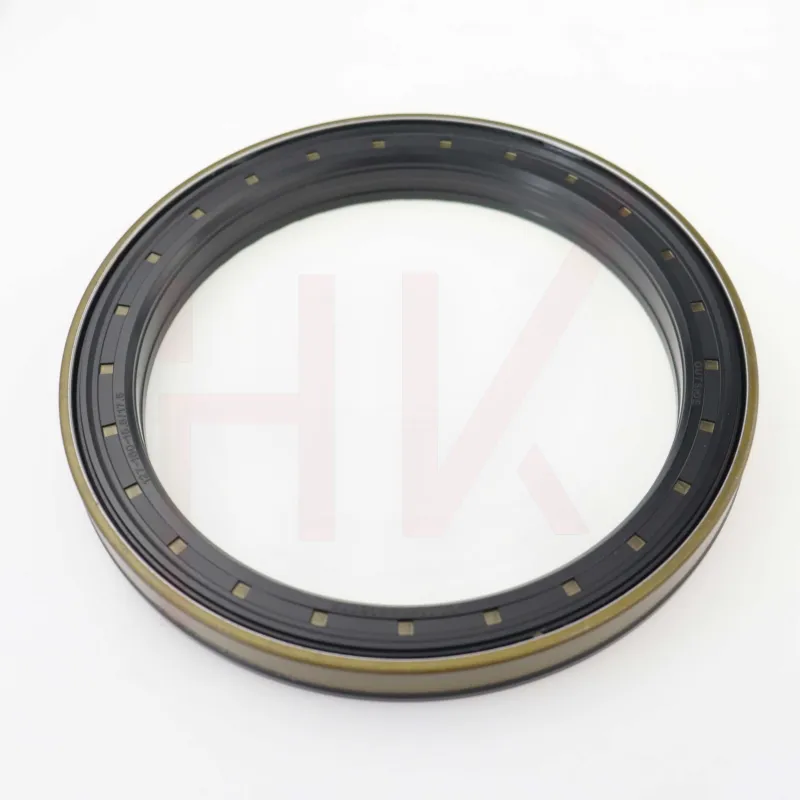
From an authoritativeness perspective, the importance of working with established manufacturers in the field of custom oil seals cannot be ignored. These manufacturers bring years of accumulated knowledge, pioneering innovations, and industry certifications to the table. Their reputations are built on consistent delivery of high-quality products and the development of bespoke solutions that cater to complex requirements. With a strong foundation in research and development, these companies often literally set the seal standards that others follow. They also provide invaluable data sheets and consultation, ensuring that the end products not only comply with industrial benchmarks but often exceed them.
custom oil seals
Trustworthiness is further evidenced through rigorous quality testing and assurance processes. Custom oil seals undergo a variety of testing methodologies—ranging from laboratory simulations of wear and tear to field tests in actual operating conditions. Such robust quality control processes guarantee that each seal can withstand the rigors it will face during its operational life. Customers can trust that a custom oil seal is built to last, reducing unexpected downtimes and maintenance costs associated with seal failure. Furthermore, long-term partnerships with trusted seal manufacturers often result in tailored maintenance schedules and support, minimizing the total cost of ownership for machinery that relies heavily on these components.
In addition to the main attributes of material choice and manufacturing expertise, modern advancements in technology have opened new frontiers in custom oil seal design. Techniques such as 3D printing for prototyping and advanced CAD software enable precise modeling and testing before manufacturing even begins. Such advancements facilitate the rapid production of seals that are not only tailor-made for existing machinery but are also easily adaptable to changing dynamics, be it an upgrade of machinery or a shift in operational processes.
For businesses, investing in custom oil seals is a strategic decision. The initial costs may be higher than standard seals, but the long-term benefits far outweigh these costs. Enhanced performance, reduced maintenance, and increased reliability of equipment translate into a stronger bottom line. Moreover, companies can leverage their use of custom oil seals as a mark of quality and commitment to excellence, thereby boosting their market reputation.
In essence, custom oil seals are not just functional components but pivotal contributors to the seamless operation of industrial machinery. They embody an amalgamation of meticulous design, material science, and engineering acumen. For industries seeking reliability and performance, custom oil seals offer a compelling proposition, reflecting the delicate balance between innovation and tradition in mechanical engineering.