Boom cylinder seal kits serve as crucial components for maintaining the functionality and longevity of heavy machinery such as excavators, backhoes, and cranes. These kits, typically comprising O-rings, backup rings, wipers, and seals, are engineered to withstand extreme pressures and environmental conditions inherent in construction, mining, and industrial applications.

Derived from materials such as nitrile rubber, polyurethane, and PTFE, boom cylinder seal kits are designed to provide robust sealing solutions that ensure hydraulic systems remain leak-proof and efficient. The functionality of these kits lies in their ability to prevent hydraulic fluid from escaping, thereby maintaining consistent pressure and reducing the risk of mechanical failure.
Choosing an appropriate boom cylinder seal kit requires expertise and understanding of the machine's operational dynamics. The selection process involves evaluating the machine's working conditions, including temperature extremes, exposure to contaminants, and operational pressure ranges. Machine operators and maintenance personnel with a deep understanding of these factors can effectively select a seal kit that complements the equipment's requirements.
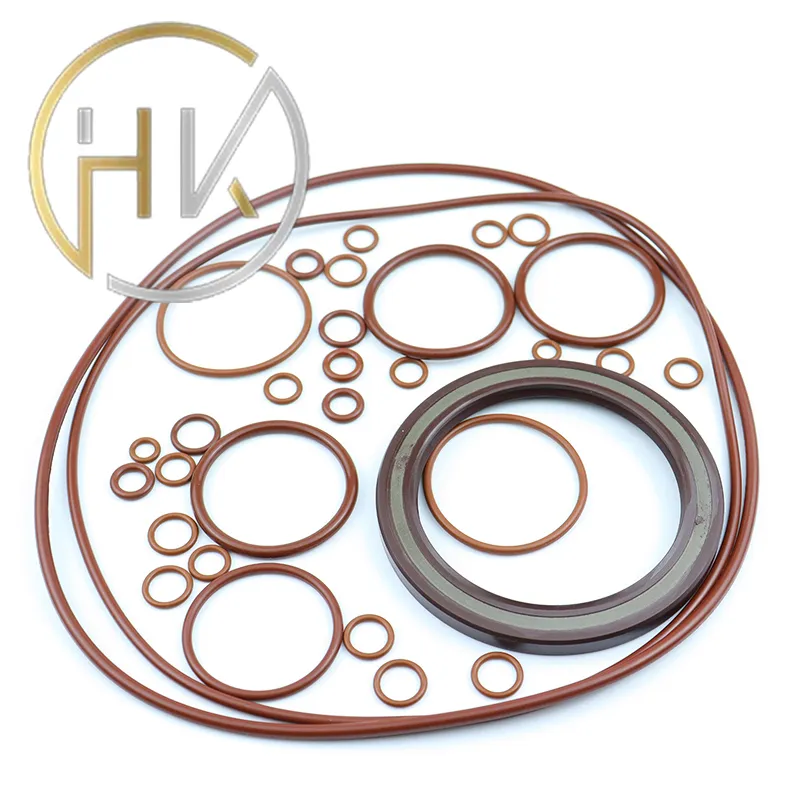
The installation process of a boom cylinder seal kit demands a meticulous approach to ensure optimal performance. Experts recommend a systematic disassembly of the cylinder, paying particular attention to avoiding damage to the piston rod and bore. Cleaning the components thoroughly of residual fluids and particles is vital to promote a clean environment for the new seals. When installing the seals, lubricating them with a compatible hydraulic fluid aids in reducing friction and wear, ensuring a snug fit and extended service life.
Regular maintenance and timely replacement of boom cylinder seals are instrumental in extending the equipment's operational life and preventing costly downtime.
Operators should schedule routine inspections, focusing on signs of wear and degradation in the seals. These inspections not only preserve the hydraulic system’s integrity but also promote safety by preventing inadvertent leaks which could lead to equipment hazards or environmental contamination.
boom cylinder seal kit
The efficacy of boom cylinder seal kits is underscored by their contribution to machine efficiency and reliability. By maintaining the integrity of the hydraulic system, these kits play an essential role in the operational effectiveness of heavy machinery, enabling tasks to be performed with precision and minimal interruption. Their durability and performance directly influence project timelines and cost-efficiency, making them a vital investment for heavy machinery operators.
Industry authorities and manufacturers often provide guidelines and resources to ensure that users understand the nuances of using and maintaining seal kits. Their expertise offers a wealth of information that includes troubleshooting common issues, understanding seal materials and compatibility, and providing insights into innovations in seal technology.
Trust in the quality and performance of boom cylinder seal kits is fostered through certifications and standards adherence, such as ISO certifications, which signify that the manufacturing processes meet international quality and safety standards. Reputable suppliers often offer warranties and satisfaction guarantees, providing further assurance of the product's reliability and effectiveness.
For professionals in the construction and industrial sectors, keeping abreast of the latest trends and advancements in seal technology is critical. Participating in workshops, seminars, and training sessions can enhance understanding and skills in dealing with boom cylinder seal kits, leading to informed decision-making and optimal equipment management.
In summation, boom cylinder seal kits are indispensable for enhancing the performance and reliability of hydraulic machinery. Their role in preventing fluid leaks, maintaining pressure, and reducing wear and tear cannot be overstated. By integrating expertise, regular maintenance, and adherence to industry standards, operators can ensure that their machinery performs at its best, maximizing productivity and minimizing operational costs.