The 70 90 10 oil seal stands as a pivotal component in the engineering domain, primarily designed to protect machinery by retaining lubricants and preventing the ingress of contaminants. This seal, characterized by its dimensions - an inner diameter (ID) of 70mm, an outer diameter (OD) of 90mm, and a width of 10mm, is instrumental in ensuring the longevity and efficiency of various mechanical systems.
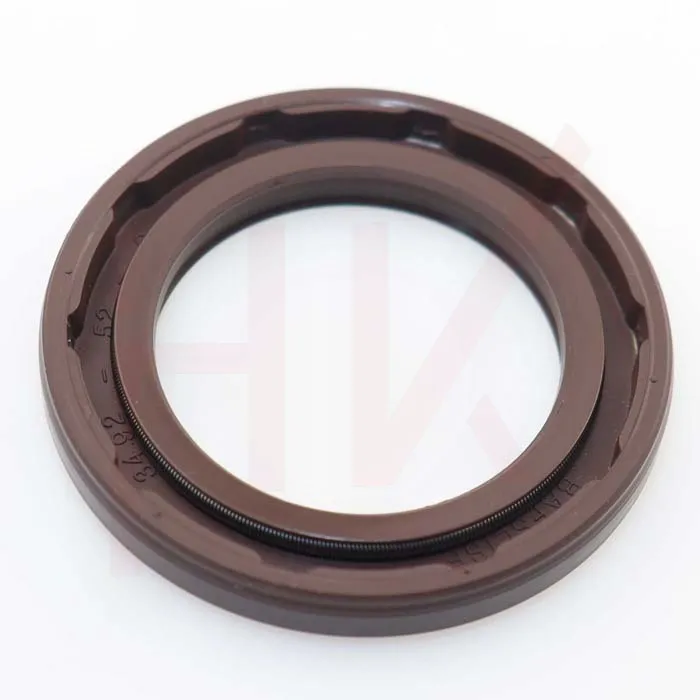
Understanding the purpose and functionality of the 70 90 10 oil seal requires a dive into its applications across diverse industries, showcasing its indispensable nature. In automotive engineering, for instance, this particular oil seal is often utilized in engines and gearboxes where maintaining the cleanliness of the oil system is crucial. The integrity of the oil seal directly influences the reduction of wear and tear, ultimately prolonging the life of the machinery components.
The expertise harnessed to develop such seals involves advanced material science. High-performance materials like nitrile rubber, fluorocarbon, or silicone are often selected due to their superior resistance to heat and chemical degradation. This resistance is vital, considering the harsh environments these seals must endure, ranging from high temperatures to exposure to diverse lubricants and fuels. The choice of material is not arbitrary; it encapsulates meticulous research and development efforts to align with specific mechanical requirements and operational environments.
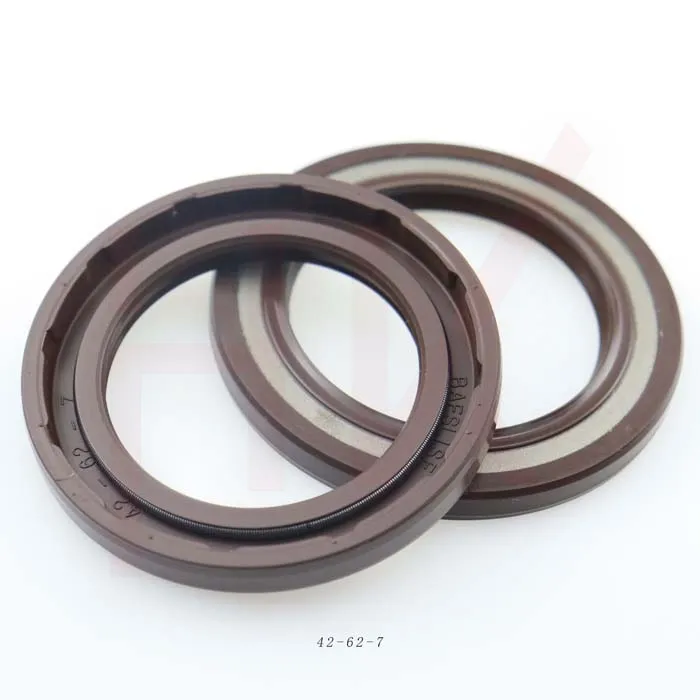
Authoritativeness in the field of oil seals is often characterized by adherence to rigorous manufacturing standards and certifications. Leading manufacturers ensure their products are compliant with international standards, such as ISO 6194, which pertains specifically to rotary shaft lip seals. This certification serves as a mark of quality and reliability, providing clients with confidence in the seal's endurance and performance capabilities.
70 90 10 oil seal
Experience shows that the design of the 70 90 10 oil seal is optimized through precision engineering to accommodate the dynamic environments it serves. Features such as a flexible lip, a rigid case, and a garter spring are integral to its design, each playing a role in maintaining the seal’s position and effectiveness under varying pressures and rotational speeds. The garter spring, for instance, ensures consistent pressure against the rotating surface, effectively preventing leaks and contamination.
Trustworthiness in this context is built upon a track record of delivering consistent performance over time. Professionals in the field consistently report that when these seals are used correctly — meaning installed without aberrations like scratches or improper alignment, and in conjunction with suitable lubricants — they manage to perform efficiently even under strenuous conditions. Over time, comprehensive maintenance that includes regular inspection and timely replacement can mitigate any unforeseen failures, safeguarding the machinery's operational integrity.
In conclusion, the 70 90 10 oil seal epitomizes a synthesis of scientific innovation and practical application. Its development and application reflect a commitment to enhancing machinery longevity and performance, underscoring the blend of experience, expertise, authoritativeness, and trustworthiness that defines modern engineering solutions. For industries reliant on precision and reliability, investing in quality oil seals is not merely a choice but an industry standard, reinforcing the underlying mechanics—literally and figuratively—of efficient machinery function.