The 35x52x7 oil seal is an essential component in various machinery and equipment, providing a barrier against contaminants while ensuring that lubricants remain contained within mechanical systems. Professionals across industries ranging from automotive to industrial manufacturing often rely on this specific size of oil seal due to its reliability and effectiveness in demanding environments.
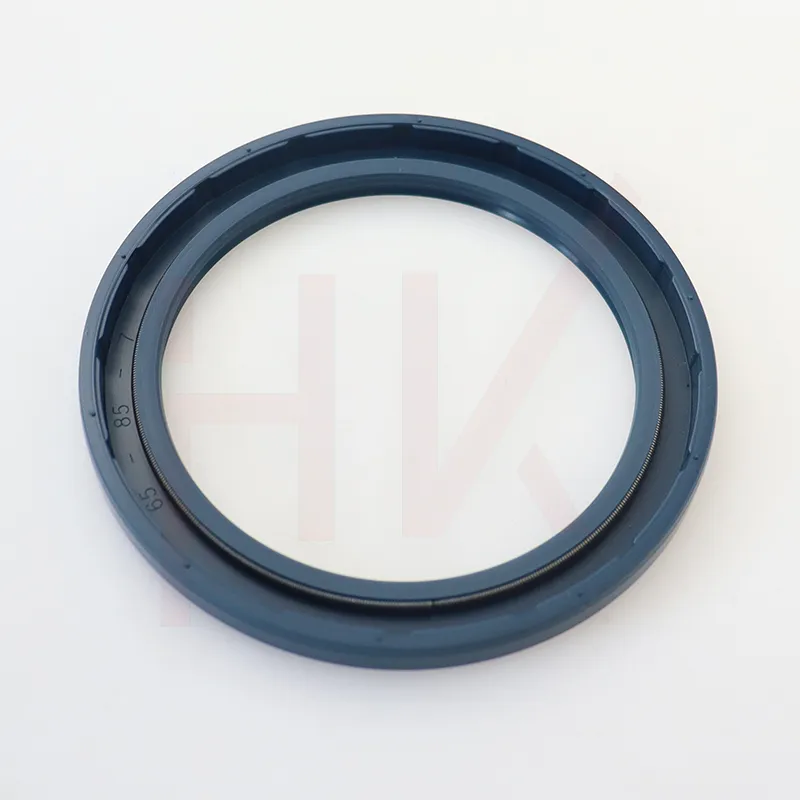
Understanding the specifics of a 35x52x7 oil seal involves recognizing the critical nature of its dimensions and materials. The first number, 35, refers to the inner diameter in millimeters, indicating the shaft size that the seal will fit. The second number, 52, specifies the outer diameter, meaning the cavity size into which it will be installed. The final number, 7, represents the width of the seal, a crucial factor in determining its contact surface and sealing ability. These dimensions are carefully chosen to provide a snug fit, minimizing the risk of leakage or seal failure under pressure.
When selecting an oil seal like the 35x52x7, material composition is paramount. Common materials include Nitrile, Viton, and Silicone, each offering distinct advantages. Nitrile is frequently used due to its excellent resistance to oils and ability to handle temperatures from -40°C to 120°C. This makes it ideal for most general-purpose applications. Viton seals, with their superior temperature tolerance (up to 250°C) and chemical resistance, are suited for more demanding applications involving exposure to harsh chemicals or higher operational temperatures. Silicone, known for its flexibility and low-temperature performance, is often used in environments where extreme cold is a factor.
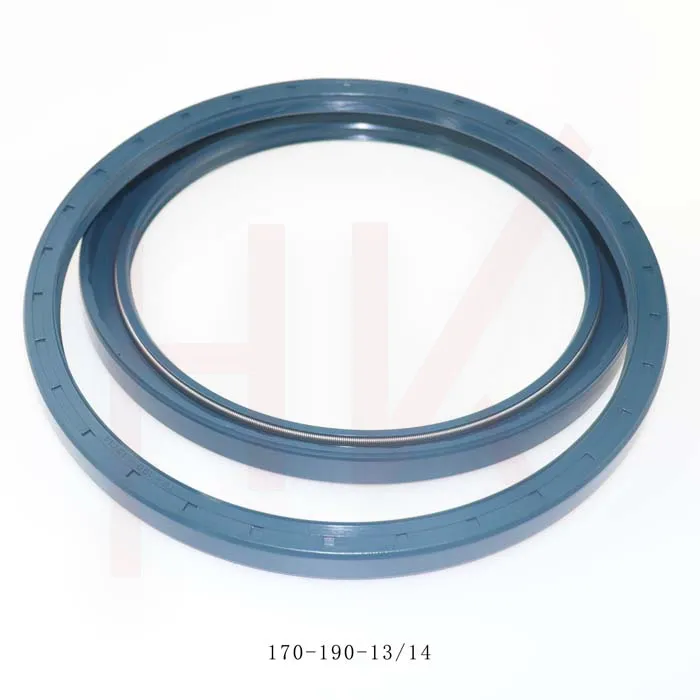
Installation precision is critical with an oil seal of this caliber. Improper installation can lead to premature seal failure, which might result in costly downtime or equipment damage. Techniques such as using an appropriate seal driver tool and ensuring a clean shaft and housing area can mitigate these risks. Additionally, lubricating the oil seal’s lip prior to installation is vital for reducing initial friction and ensuring smooth operation.
One of the standout features of the 35x52x7 oil seal is its versatility across different machinery. In automotive applications, it is commonly used in engines and gearboxes, where it plays a key role in preventing oil leaks that could lead to mechanical wear or environmental contamination. In industrial settings, it finds use in pumps, compressors, and turbines, among others, safeguarding these systems against the ingress of dust, moisture, and other potential pollutants.
35x52x7 oil seal
The long-term reliability of the 35x52x7 oil seal is highly regarded in the engineering community. Its ability to maintain effective sealing under diverse conditions is backed by rigorous testing and quality standards that meet international benchmarks. Manufacturers often perform tests like accelerated life tests and pressure resistance evaluations to ensure durability and performance consistency over time. This commitment to quality is crucial for industries that rely on uninterruptible operation to maintain productivity and safety.
Moreover, maintenance practices play a critical role in enhancing the life span of 35x52x7 oil seals. Regular inspections for signs of wear, such as hardening, cracking, or excessive swelling, can determine the need for replacement before failure occurs. Adopting a proactive maintenance strategy not only improves equipment longevity but also optimizes operational efficiency by preventing unforeseen breakdowns.
The reputation of the 35x52x7 oil seal is built on years of successful use cases and positive feedback from industry professionals. Technical support and after-sales services provided by reputable manufacturers further bolster trust. These services may include detailed product specifications, expert installation guides, and responsive customer assistance, ensuring that users have all the necessary resources to maximize their seal’s efficacy.
In conclusion, the 35x52x7 oil seal stands out as a critical component, designed to meet the rigorous demands of modern mechanical applications. Its precise dimensions, material versatility, and robust performance make it a reliable choice for maintaining system integrity across multiple industries. By ensuring proper installation and adhering to regular maintenance protocols, businesses can leverage the full benefits of this indispensable sealing solution, safeguarding their operations and reinforcing trust in their equipment’s reliability.