The 35x52x7 oil seal is a critical component in a myriad of industrial applications, ensuring the longevity and efficiency of mechanical systems. Its importance can never be understated given its role in preventing leaks, maintaining pressure, and protecting systems from external contaminants. Understanding the nuances and benefits of this specific oil seal size can help businesses and engineers make informed decisions, optimize their machinery, and ensure operational excellence.
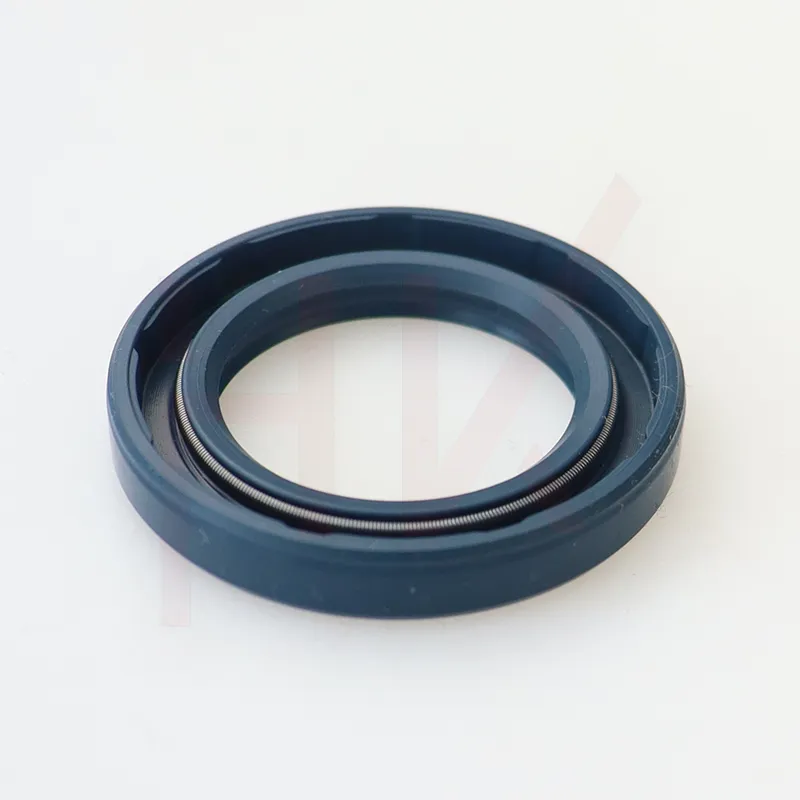
The design of the 35x52x7 oil seal reveals its purpose and functionality. With a 35mm inner diameter,
a 52mm outer diameter, and a 7mm width, it is designed to fit seamlessly into specific cavities, ensuring that the seal is snug and effective. This dimension is within a standard range that is frequently utilized in a myriad of machinery, from automotive engines to hydraulic systems, due to its ability to provide efficient sealing capabilities in a compact space.
The material composition of these oil seals typically involves a combination of nitrile rubber (NBR), polytetrafluoroethylene (PTFE), or silicone, each offering unique properties to meet varying operational demands. NBR, for instance, is known for its excellent resistance to wear and tear, compatible with various lubricants, and affordable cost. PTFE, on the other hand, offers exceptional resistance to high temperatures and harsh chemicals, making it ideal for more extreme environments. Meanwhile, silicone provides excellent flexibility and temperature stability, often used in applications where temperature fluctuations are frequent. Selecting the right material is crucial as it directly impacts the seal’s durability, efficiency, and suitability for the intended application.
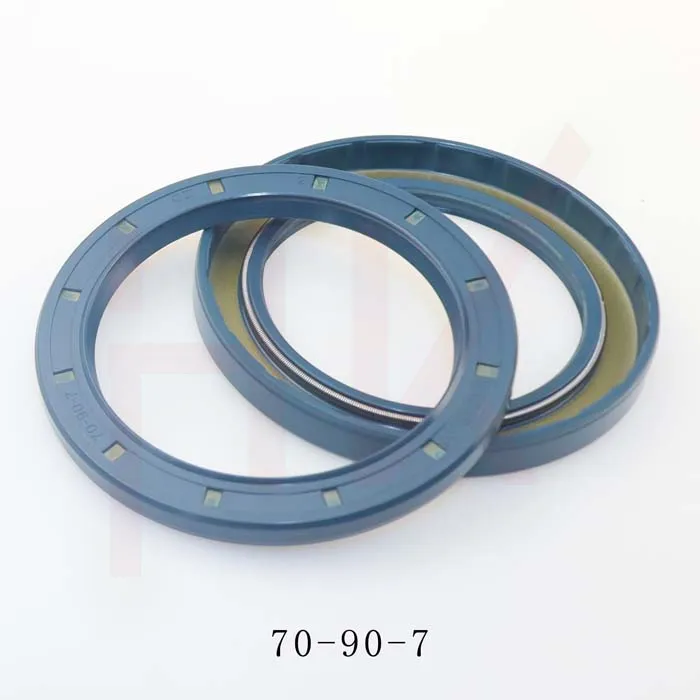
In practical scenarios, the 35x52x7 oil seal is often used in automotive gearboxes and differentials, heavy machinery, agricultural equipment, and even household appliances. Its efficiency in these applications is attributed to its capability to retain lubricants which, in turn, reduce friction, wear, and overheating. This ensures that moving parts operate smoothly, enhancing the longevity of the equipment, reducing the frequency of maintenance, and thereby lowering operational costs.
35x52x7 oil seal
One great advantage of incorporating 35x52x7 oil seals into mechanical systems is their user-friendly installation process. Typically, these seals are designed for easy insertion, with some models featuring a lip design that aids in precise positioning while providing extra sealing action. It is vital during installation to ensure that the seals are not pinched or damaged, as this could compromise their ability to prevent leaks. Tools such as seal drivers or mandrels are often recommended to facilitate proper installation, extending the operational life of the seal.
In terms of expertise, understanding the failure modes of oil seals is crucial for both diagnostics and preventive maintenance. Common issues include hardening, cracking, or abrasiveness of the seal material, often caused by thermal degradation, chemical attack, or simply wear and tear over time. By familiarizing oneself with these potential issues, maintenance can be more effectively scheduled and performed, avoiding unforeseen failures and the subsequent costly downtime.
Trustworthiness in the performance of 35x52x7 oil seals can also be heavily influenced by the manufacturer’s reputation. Leading manufacturers in the market ensure that their oil seals meet stringent quality standards, which are often validated by certifications such as ISO 9001. This ensures not only reliability but also compatibility across different operational environments. Investing in seals from reputable manufacturers provides peace of mind, supported by warranties and comprehensive customer support, which can prove invaluable over the seal’s lifecycle.
In conclusion, the 35x52x7 oil seal is more than just a small component within a larger mechanism. Its role is indispensable, directly impacting the performance and reliability of equipment across several industries. By meticulously selecting the right material, ensuring precise installation, and partnering with trusted manufacturers, businesses can capitalize on their mechanical efficiency while minimizing risks and costs associated with unexpected downtimes or equipment failures. This approach not only reinforces operational trustworthiness but also aligns with best practices in mechanical maintenance and efficiency.