When it comes to the industrial sector, efficiency and reliability are paramount. In industries that rely heavily on machinery, even the smallest components can have a significant impact on performance and longevity. One such critical component is the oil seal, designed to keep lubrication intact while preventing contaminants from entering a machine. Focusing on the combination — 35 72 10 oil seal — not only highlights precision but also brings attention to a specific, often-overlooked element that enhances mechanical efficiency.
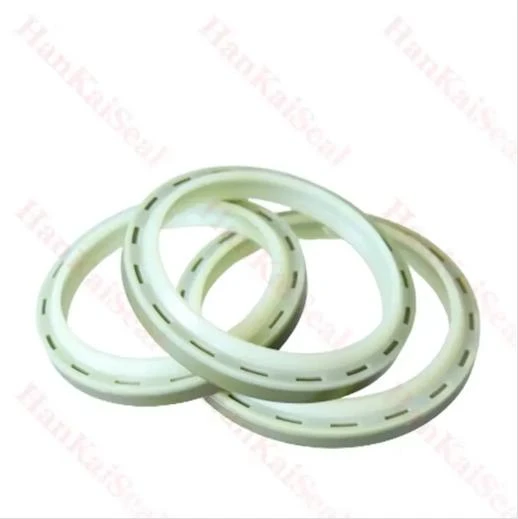
An oil seal, often referred to as a shaft seal, rotary seal, or grease seal, is a crucial component in any piece of machinery that involves rotary motion. The numbers 35 72 10 represent the dimensions of the oil seal in millimeters the inner diameter, outer diameter, and thickness, respectively. These measurements are meticulously engineered to provide an exact fit, allowing the seal to perform its duties under demanding conditions.
Experience with these specific dimensions, 35 72 10, shows their adaptability across various applications, particularly in automotive and industrial machines. Engines, gearboxes, pumps, and compressors often utilize this size, underscoring their versatility. The precision of these dimensions ensures the seal sits securely in its housing, maintaining the correct amount of pressure on the rotating shaft while minimizing wear and tear.
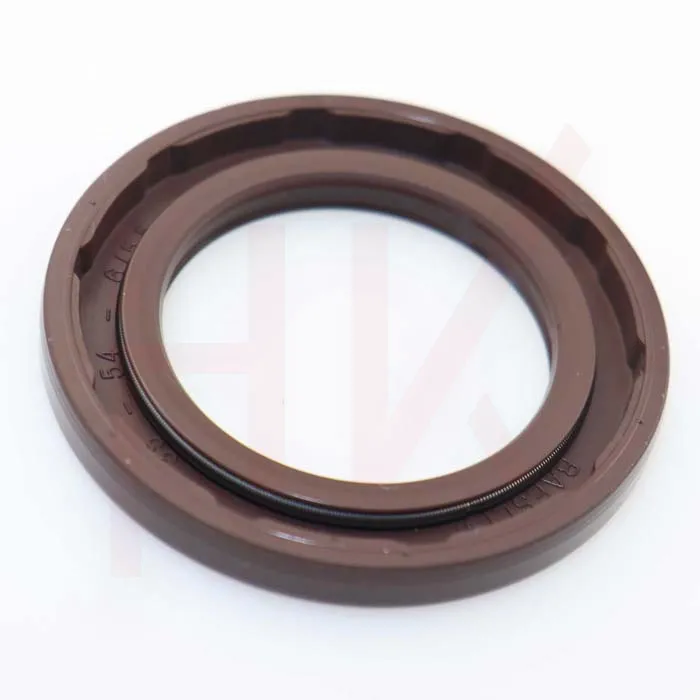
Expertise in the field of oil seals reveals the delicate balance required in balancing friction reduction with sealing capability. Material selection plays a vital role in this balance. For 35 72 10 oil seals, rubber is often the material of choice due to its flexibility, resilience, and chemical resistance. Nitrile rubber (NBR) is widely used, favored for its durability and ability to withstand temperature variations while resisting oils and greases. However, for applications requiring higher temperatures or specific chemical resistances, alternatives like Viton—a high-performance fluoroelastomer—may be used for superior longevity and effectiveness.
35 72 10 oil seal
The authoritativeness of this critical component is reflected in the rigorous testing and quality standards met by manufacturers specializing in seals. Industry leaders rely on extensive R&D to innovate new seal designs that can cope with ever-increasing demands for efficiency and compactness in machinery. Computer-aided design (CAD) and extensive prototyping ensure that each seal meets operational specifications before it reaches the market. Adherence to ISO standards in production further underscores the reliability and credibility of these seals, assuring users worldwide of their quality.
Trustworthiness with the 35 72 10 oil seals is evidenced by both historical performance and user testimonials. Many industries have noted significant reductions in unscheduled maintenance due to failure of these components. Users across sectors consistently report increased machine uptime and lower total cost of ownership as the seals perform seamlessly under diverse conditions over extended periods. Additionally, reputable manufacturers offer comprehensive warranties and support, ensuring that clients receive guidance and service whenever necessary.
The integration of 35 72 10 oil seals in a system not only prevents leaks but also acts as a shield against environmental contaminants such as dust and water vapor, thereby preserving the integrity of the lubricant. This intrinsic quality extends the lifespan of machinery, promotes reliability, and reduces operational costs. Moreover, their role in enabling efficient energy transfer between moving parts is fundamental to optimizing machine performance and reducing energy expenditures.
In conclusion, the importance of the 35 72 10 oil seal cannot be understated in the lexicon of mechanical components. It embodies the confluence of precision engineering, material science, and industrial reliability. Whether it's augmenting the performance of an engine or ensuring the efficiency of a hydraulic system, these seals represent an indispensable element in the fabric of modern engineering. Industry professionals who prioritize reliability and efficiency understand that even a minor component like an oil seal can have major impacts on productivity and operational excellence.