An oil seal, often an overlooked component in machinery, plays an indispensable role in safeguarding vital mechanical systems. The 30x42x7 oil seal, precision-engineered with specific dimensions (30mm inner diameter, 42mm outer diameter, and 7mm width), is quintessential for numerous applications ranging from automotive engines to industrial machinery.
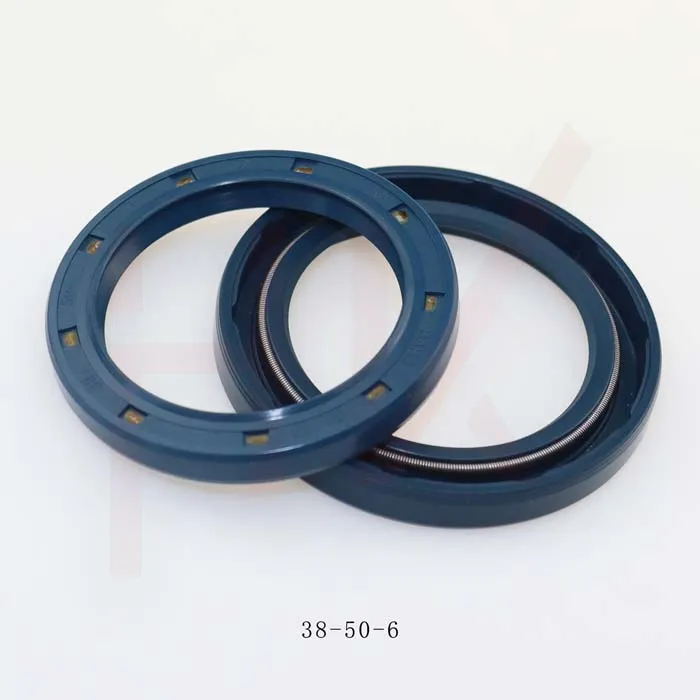
Why exactly does the 30x42x7 oil seal stand out? Its unique size makes it an ideal solution for compact systems where efficient sealing is paramount. While it may seem like a trivial piece in the grand scheme, its performance directly impacts an entire machine's longevity and functionality.
From a professional standpoint, the importance of understanding the specific material composition and design of the oil seal cannot be understated. Typically, manufacturers opt for materials like nitrile rubber (NBR), fluorocarbon (Viton), and silicone, each serving distinct purposes. NBR is favored for its excellent resistance to petroleum-based oils, while Viton is optimal for high-temperature and chemically harsh environments. Silicone seals, on the other hand, excel in extreme temperature conditions, making them versatile yet highly specialized for select applications.
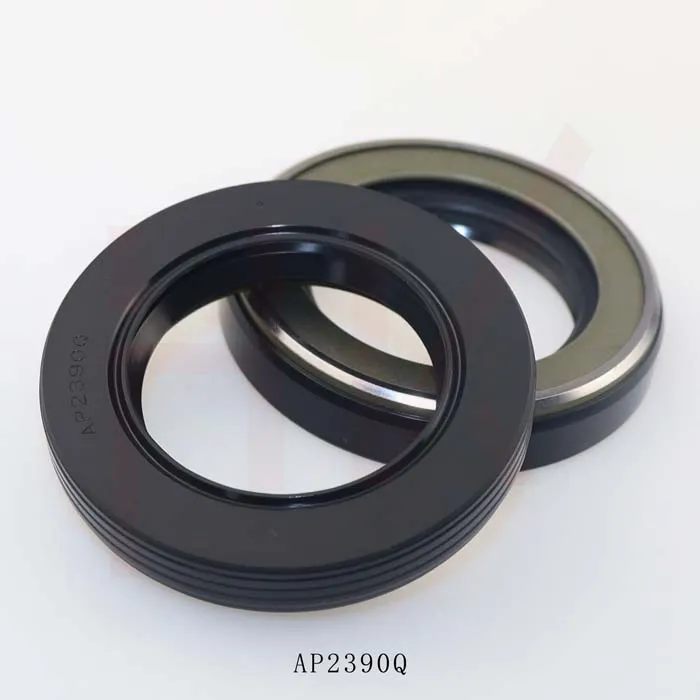
The expertise in utilising the 30x42x7 oil seal involves recognizing its operational limits and axially loaded environments. This seal is engineered for low to medium-duty applications, often found in gearboxes, electric motors, and small pumps. The lip design on the seal's interior is a crucial factor in its ability to withstand pressure differentials and resist leakage.
Authoritativeness in the use of oil seals can be attributed to adhering to manufacturer specifications and learning from industry standards.
ASTM and ISO guidelines are pivotal in evaluating oil seal performance. These standards ensure the seal's ability to resist wear, prevent contaminants from entering the system, and maintain oil within systems, thereby validating the seal's reliability under specified conditions.
30x42x7 oil seal
Trustworthiness in dealing with oil seals may seem abstract, but it hinges on choosing credible suppliers and conducting regular assessments of seal condition. Accountability is reflected in the meticulous installation process—where even a slight misalignment or contamination can lead to premature failure and system downtime. Choosing seals from reputable manufacturers with traceable quality control can mitigate these risks, ensuring that each seal meets the operational demands it is subjected to.
Field experience dictates that proactive maintenance extends the life of the 30x42x7 oil seal. Regular inspections for signs of wear such as hardening, cracking, or flattening of the seal lip can preemptively prevent system failure. Proper lubrication during installation aids in achieving a reliable seal an overlooked step that can significantly impact performance.
A case in point involves a manufacturing facility that experienced recurrent machinery stoppages. Investigation revealed the root cause as substandard seals that inadequately handled the system's pressure dynamics. By switching to premium 30x42x7 oil seals, specially crafted for their operational environment, the facility observed a dramatic reduction in downtime and maintenance costs.
In conclusion, the 30x42x7 oil seal, though small, embodies the critical balance of expertise, precision, and reliability. Understanding its role and intricacies contributes to significant performance improvements and operational efficiency in a diverse array of industrial applications. Optimal results rely on employing the right seal tailored to specific conditions, underscoring the importance of informed selection and diligent maintenance practices. With proven authority and a foundation of trust, these seals ensure systems run smoothly, thereby protecting investments and sustaining productivity.