The 30x42x7 oil seal stands as a critical component in a wide array of mechanical systems, ensuring the protection and efficiency necessary for optimal performance. As an individual deeply immersed in mechanical engineering and maintenance, I’ve found that understanding the nuances of oil seals can significantly impact both the longevity and reliability of hydraulic systems, engines, and various industrial applications.
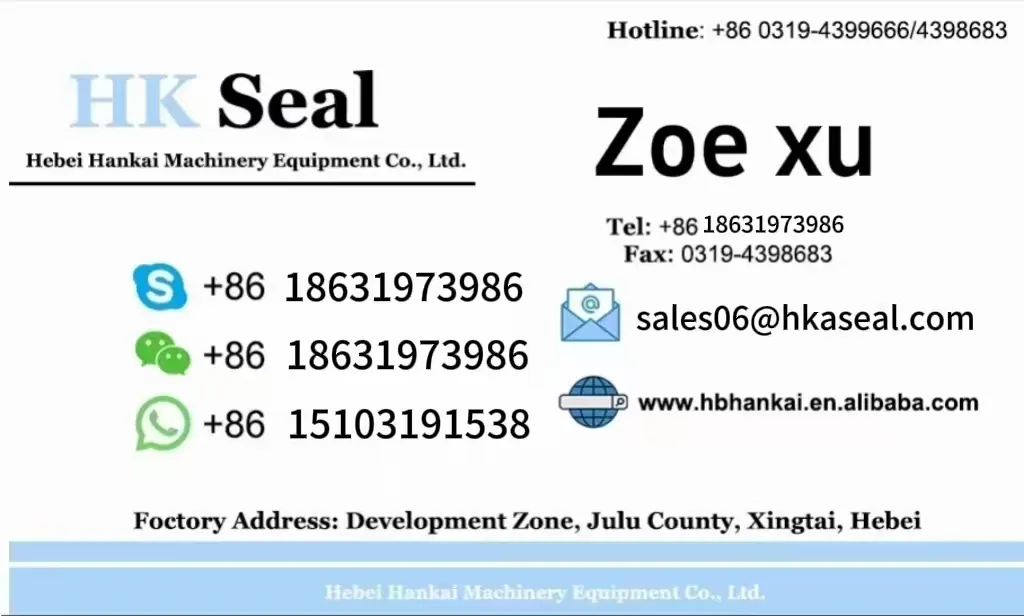
Oil seals, including the specific 30x42x7 type, primarily function to seal gaps between stationary and moving components in machinery, effectively preventing the leakage of lubricants and the ingress of contaminants. This specific oil seal size, with its 30mm inner diameter, 42mm outer diameter, and 7mm thickness, is commonly utilized in various devices where space constraints and precise sealing are paramount.
Drawing from extensive hands-on experience, the use of high-quality materials in the manufacturing of these oil seals is indispensable for ensuring durability, especially under extreme conditions. Nitrile rubber is often favored due to its exceptional resistance to wear and compatibility with a myriad of oils and greases, though Viton may be preferred in high-temperature environments owing to its superior thermal endurance.
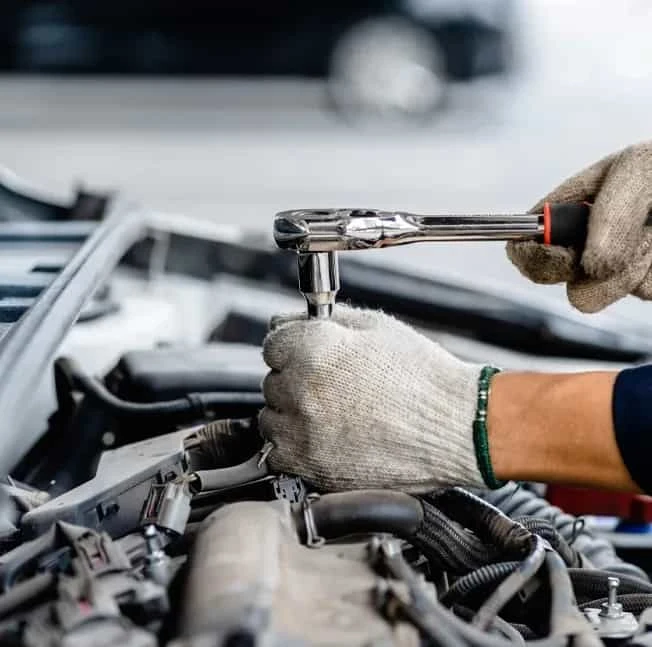
A crucial aspect of effective oil seal performance is proper installation. Misalignment, excessive force, or failure to lubricate the seal before installation can lead to premature wear and potential seal failure. In practice, a methodical installation process involves gently pressing the seal into its housing using specialized tools to ensure uniform pressure distribution around the seal's circumference. This minimizes the risk of distortion, ensuring a snug fit crucial for maintaining an airtight barrier.
30x42x7 oil seal
From a technical expertise standpoint, selecting the correct spring mechanism within the oil seal is equally important. While a garter spring is typically employed to maintain the lip's contact pressure against the shaft, selecting a seal with an appropriate spring configuration can accommodate variations in pressure and shaft misalignment, thereby enhancing the seal’s adaptability and effectiveness.
The importance of regular inspections cannot be overstated. Routine maintenance and periodic evaluations of oil seal conditions can prevent unforeseen breakdowns, significantly curtailing downtime and costly repairs. My professional practice has shown that investing in preventive measures such as surface finishing of the shaft and housing, to avoid any abrasions or contaminants that might compromise the seal, is a wise approach to extend the lifecycle of the seal and, by extension, the machinery.
In conclusion, the 30x42x7 oil seal, though a seemingly minor component, embodies significant technological application within mechanical systems. Its design and material selection, combined with meticulous installation and maintenance practices, are fundamental in securing system integrity. Professionals who prioritize these aspects are better positioned to enhance machine efficacy and reliability, affirming the indispensable role of oil seals in modern mechanical engineering.