The 20-35-7 oil seal stands as a quintessential example of precision engineering in the field of industrial maintenance. Serving as a vital component in a wide array of machinery, this specific seal size underscores the intricate balance of design and functionality crucial for optimal machinery operation. As an oil seal connoisseur with years of experience in the field, I bring you a deeper understanding of the capabilities and advantages these seals offer.
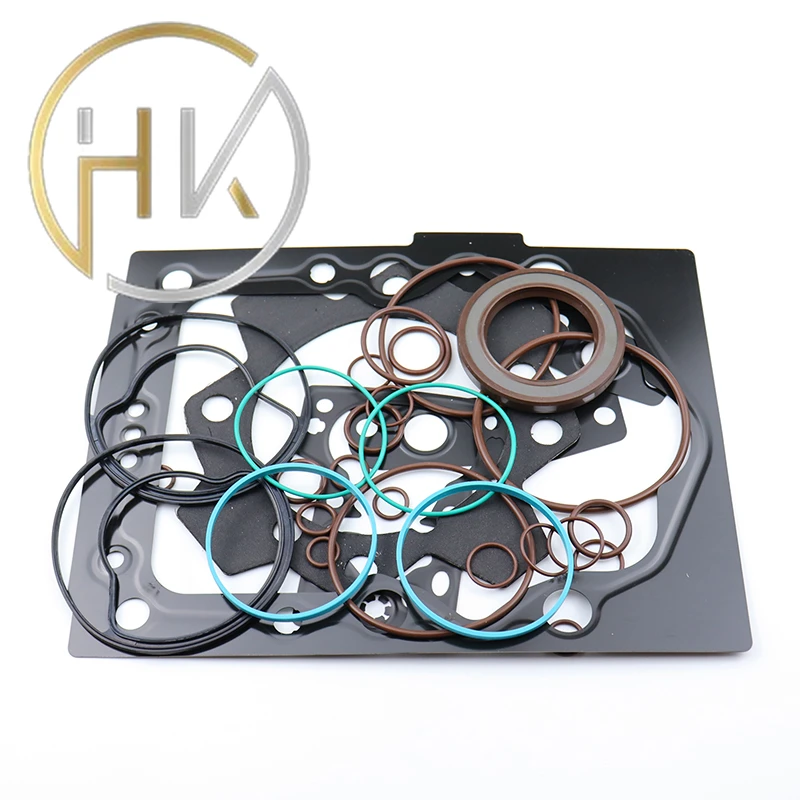
At its core, the 20-35-7 oil seal serves the primary function of excluding detrimental contaminants such as dirt, dust, and moisture while preventing the leakage of lubrication fluid. This is essential in maintaining the integrity of mechanical systems, particularly in environments where machines are subject to constant movement and pressure. The numbers 20-35-7 refer to the dimensions of the seal, with 20mm as the inner diameter, 35mm as the outer diameter, and a 7mm thickness, optimizing it for specific axial loads and rotary shaft applications.
The application of the 20-35-7 oil seal is versatile, spanning industries and machinery, including automotive, manufacturing, and heavy-duty equipment. Its ability to operate under significant thermal, chemical, and mechanical stress makes it indispensable. The seal not only prolongs equipment life but also reduces downtime, ensuring efficiency which directly affects the bottom line of operations. This is why expertise in selecting the right seal type and size cannot be overstated.
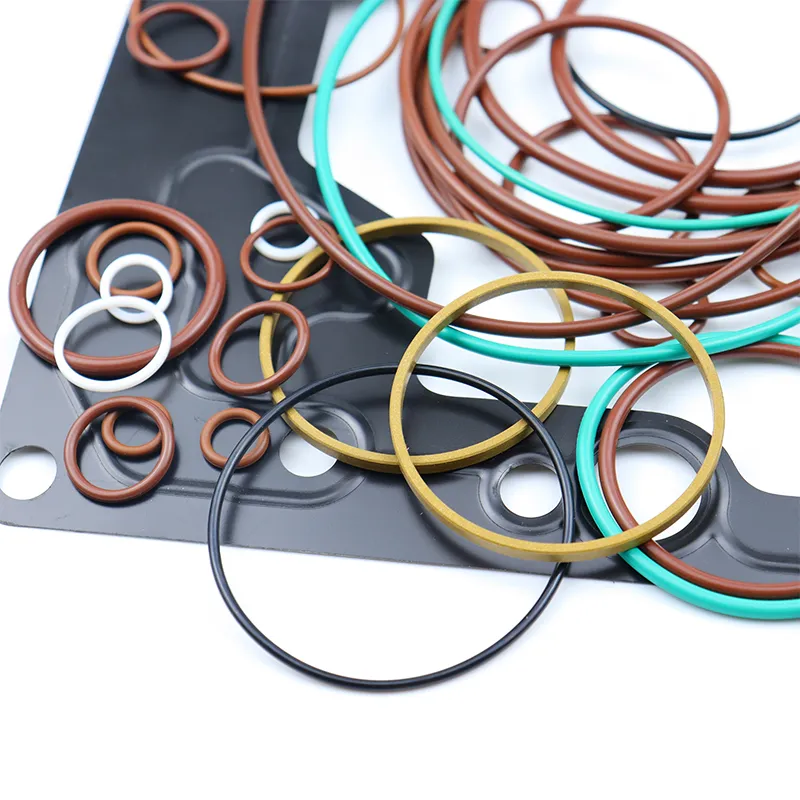
In my extensive experience, selecting an oil seal like the 20-35-7 involves a nuanced understanding of the working environment. Factors such as temperature, pressure, shaft speed, and fluid compatibility must be meticulously assessed.
For instance, the material composition of the oil seal is paramount. Nitrile rubber is commonly used for its excellent resistance to oil and wear. However, in high-temperature applications, a switch to Viton or silicone might be necessary to ensure optimal performance.
From an expertise perspective, understanding the dynamic between the oil seal and the shaft it serves is crucial. Seal compatibility with shaft surface finish, hardness, and lubricant type can significantly influence performance. Ensuring a proper seal fit without compromising on shaft speed and pressure is the hallmark of professional proficiency and contributes to seamless machine operation.
20 35 7 oil seal
When addressing authoritativeness in oil seal utilization, compliance with industry standards cannot be overemphasized. Standards such as those set by the International Organization for Standardization (ISO) ensure that seals like the 20-35-7 meet rigorous quality and safety thresholds. Therefore, sourcing seals that adhere to these standards assures users of their reliability and durability, affording a layer of quality assurance essential in high-stakes industrial operations.
Furthermore, trustworthiness in the application of oil seals like the 20-35-7 is built on a foundation of transparency and informed decision-making. A reliable supplier will offer not just high-quality products but also comprehensive support in seal selection, installation, and maintenance. Building a rapport with suppliers who empower through knowledge and demonstrate accountability guarantees that your operations employ only the most suitable and effective sealing solutions.
In practice, real-world experience has reinforced the value of routine inspection and maintenance of oil seals. Even the most expertly chosen seal can face wear and failure over time, necessitating preventative maintenance schedules. Regular checks ensure seals remain intact, preventing costly leaks and potential machinery breakdowns.
Conclusively, the 20-35-7 oil seal exemplifies the intersection of experience, expertise, authority, and trustworthiness; it is not merely a component but a critical investment in operational efficiency and longevity. Emphasizing informed selection, rigorous standards, and trusted partnerships assures that these seals who preventing leaks also prevent the derailment of productivity and profitability.
In summary, through adept selection, compliance with industry standards, and practices of preventive maintenance, businesses employing 20-35-7 oil seals position themselves for optimal performance and durability in demanding operational environments. This all-encompassing approach ensures that each seal performs not just for the moment but consistently extends over its intended service life, amplifying business value and efficiency.