In the world of industrial machinery and automotive engineering,
the role of an oil seal cannot be overstated. The specific oil seal with the keyword 20 30 7 signifies precise dimensions, indicating a bore size of 20 mm, an outer diameter of 30 mm, and a width of 7 mm. These seals are designed to protect critical components by ensuring effective sealing of lubricants within mechanical systems, and they are indispensable in maintaining the efficiency and longevity of various machines.
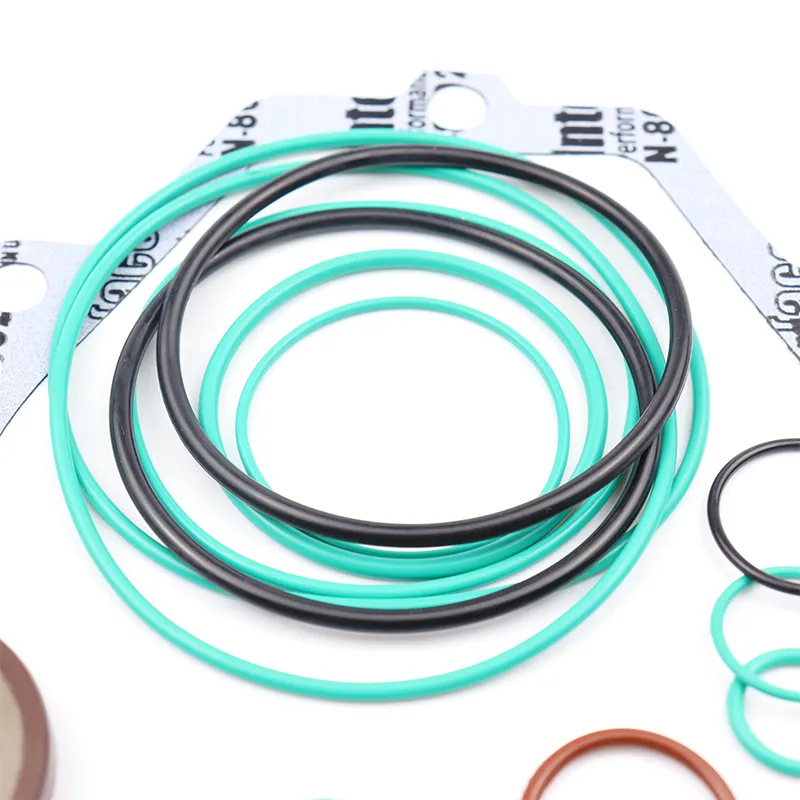
I. Understanding the Functionality of Oil Seals
Oil seals, often referred to as rotary shaft seals or lip seals, are fundamental components that serve the critical function of preventing the leakage of lubricants. By keeping the lubricant contained, they prevent dirt, dust, and moisture from entering the machinery, thus safeguarding internal components from premature wear and potential damage. The 20 30 7 oil seal is specifically tailored for smaller shaft sizes, making it ideal for use in compact machinery and automotive engines where space is limited and efficiency is paramount.
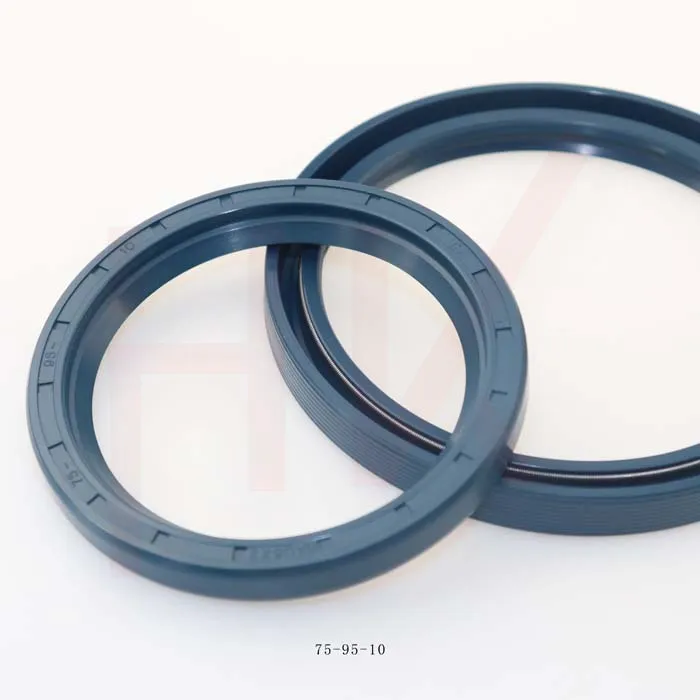
II. Expert Insights into Material Selection
Selecting the right material for an oil seal is crucial for ensuring compatibility with the operating environment. Common materials include nitrile rubber (NBR), fluoroelastomer (FKM), and silicone, each offering distinct properties. For example, NBR is renowned for its excellent resistance to petroleum-based oils and is ideal for applications with standard temperature ranges. In contrast, FKM provides superior heat and chemical resistance, making it suitable for more demanding conditions. Understanding the operating conditions and fluid compatibility is key to choosing the right oil seal material.
III. Installation Precision
The performance of an oil seal is significantly influenced by the accuracy of its installation. A seal that is misaligned or improperly fitted can fail, leading to leaks and potential equipment failure. Therefore, it is essential to ensure that the shaft and housing dimensions strictly comply with the specifications of the oil seal. Regular maintenance and inspection can help detect early signs of wear, ensuring timely replacement and uninterrupted operation. Professionals recommend using proper tools and adhering to manufacturer guidelines during installation to maximize the seal's longevity and effectiveness.
20 30 7 oil seal
IV. Case Studies and Real-World Applications
Numerous industries, from automotive to manufacturing, rely heavily on oil seals for the smooth operation of their equipment. In the automotive sector, the 20 30 7 oil seal finds common application in small engines, providing dependable performance in harsh environments. Similarly, in the manufacturing industry, these seals are often used in pumps, gearboxes, and other machinery components, where maintaining the integrity of the lubricant is crucial for operational efficiency.
V. Authority in Oil Seal Manufacturing
Selecting a reputable manufacturer is as critical as choosing the right oil seal dimensions and materials. Leading manufacturers adhere to stringent quality control processes, employing state-of-the-art technology in their production lines. They offer not only high-quality products but also technical support and expert consultations, ensuring that customers acquire the ideal sealing solutions for their specific needs.
Conclusion
When it comes to maintaining the operational integrity of machinery, the 20 30 7 oil seal plays an indispensable role. Understanding the nuances of its functionality, material selection, and installation can significantly enhance the performance and lifespan of any mechanical system. By collaborating with industry leaders and focusing on regular maintenance, businesses can foster a reliable and efficient operational environment, underscoring the importance of experience, expertise, authoritativeness, and trustworthiness in the world of oil seals.