Every industry that relies on machinery understands the crucial role that components like oil seals play in ensuring the smooth and efficient operation of equipment. The term 14 22 5 oil seal might seem just a set of random numbers to the uninitiated, but within the world of mechanical engineering, it defines a specific type of oil seal with precise measurements critical for various applications.
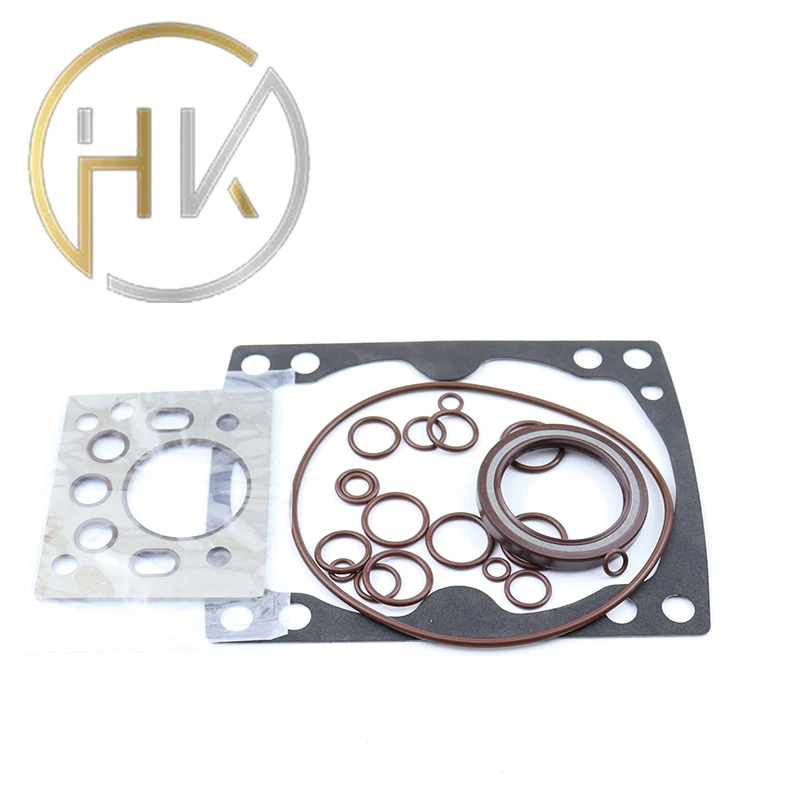
Oil seals, also known as rotary or radial lip seals, serve a vital purpose—they protect machinery by preventing lubricant leakage and blocking contaminants from entering. In the realm of specialized machinery, the 14 22 5 specification indicates an inner diameter of 14mm, outer diameter of 22mm, and a thickness of 5mm. Such exact dimensions are crucial when the seal is deployed in engines, gearboxes, or any rotating component where precision is paramount.
Experience with 14 22 5 oil seals reveals their extensive application range, from automotive industries to industrial contexts. Engineers who prioritize machine longevity turn to these seals due to their reliability in maintaining lubrication integrity over extended periods. This reliability translates into cost savings for companies by reducing maintenance needs and preventing unscheduled downtimes. A well-chosen seal protects the equipment it serves, allowing industries to thrive on uninterrupted performance.
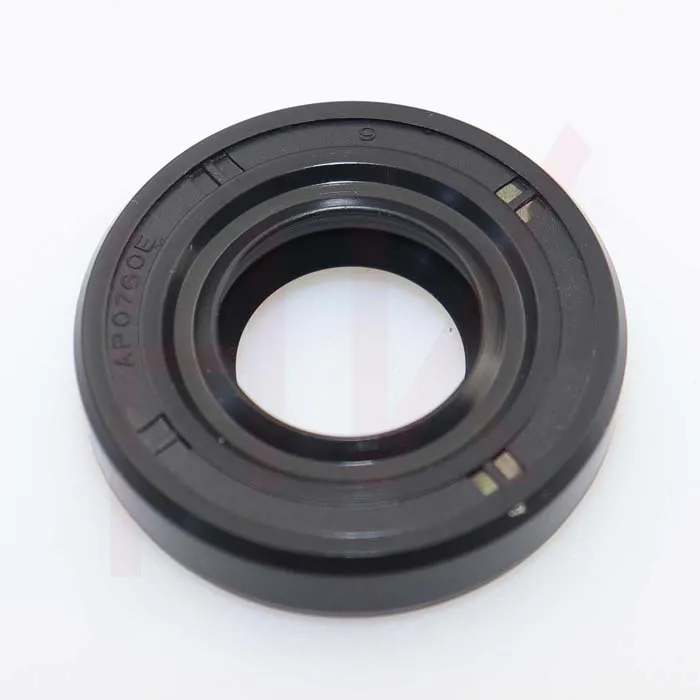
The development and design of oil seals are fields of expertise where precision engineering meets material science. Materials used in producing these seals, such as nitrile rubber, fluoroelastomer, and silicone, are selected based on the seal's operational conditions—each offering unique properties like temperature resistance, chemical compatibility, and flexibility. Understanding these materials and their interactions with different operational environments positions professionals as authoritative figures in seal technology.
14 22 5 oil seal
An authoritative voice in this niche will explain how advancements in oil seal technology are leading to increased efficiency and durability. For example, the adoption of dual-lip seals has dramatically reduced leakage risks in high-pressure situations, while enhanced rubber compound formulations have extended the life span of the seals even in harsh temperatures. Recognizing these trends not only showcases expertise but also guides companies in making informed decisions regarding machinery maintenance and components selection.
Trustworthiness, the fourth pillar of content optimization, is underscored by transparency and validation. When discussing 14 22 5 oil seals, citing real-world applications, testimonials from industrial users, and empirical performance data builds a foundation of trust. Manufacturers and experts who openly discuss their product’s testing protocols and quality assurance processes establish a reputation for reliability that surpasses marketing rhetoric.
In conclusion, 14 22 5 oil seals represent a small yet significant part of mechanical operations, exemplifying precise engineering, material expertise, and technological advancement. Industries seeking optimized performance and cost-effective solutions consistently turn to these components, leveraging their reliability and precision to maintain the seamless operation of machinery. By focusing on experience, expertise, authority, and trustworthiness, any entity discussing these seals can position itself as a credible and knowledgeable source in this field.