When it comes to ensuring the longevity and efficiency of mechanical equipment, understanding the nuances of components such as the 12x22x7 oil seal is crucial. This seemingly small part plays a pivotal role in the integrity and functionality of diverse machinery, from automotive engines to industrial machines.

The 12x22x7 oil seal is specifically designed to fit applications requiring a precise fit within a 12 mm shaft, a 22 mm bore, and a 7 mm length. Its primary function is to prevent lubricant leakage while simultaneously protecting against the ingress of contaminants. This is vitally important in mechanical systems where maintaining the integrity of the lubrication system can significantly extend the service life of the machine.
Drawing from professional experience, one cannot overstate the expertise required to choose the right oil seal. The material composition of the seal is a decisive factor in its performance. Typically, these seals are made from materials like Nitrile Rubber (NBR), Fluoroelastomer (FKM), or Silicone, each offering unique advantages. Nitrile rubber, for instance, offers excellent resistance to oils and fuels, making it ideal for automotive applications. Fluoroelastomer provides superior chemical resistance and operates efficiently at high temperatures, thus suitable for industrial machines subjected to extreme conditions.
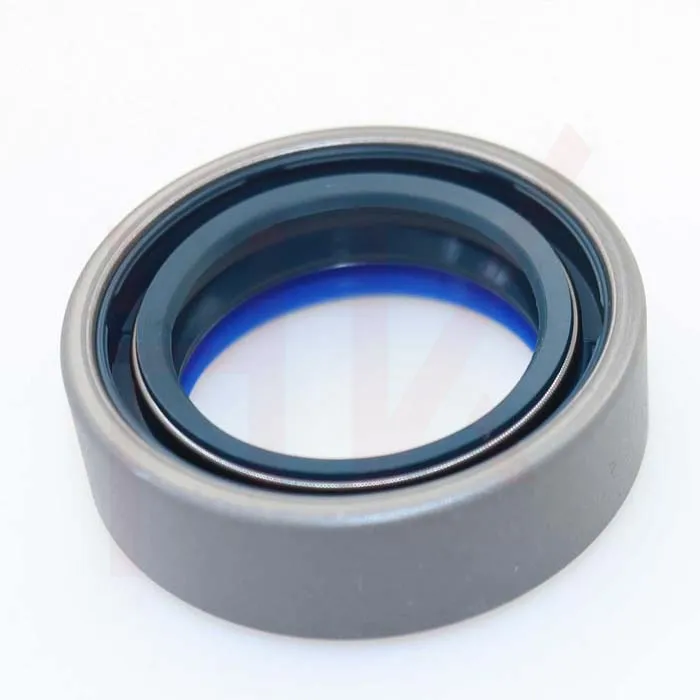
Authoritativeness in oil seal selection comes from a deep understanding of the working environment of the machinery. For instance, equipment exposed to high temperatures or aggressive substances demands oil seals that can maintain integrity without degradation. A failure to match the oil seal material to the operating conditions can lead to premature seal failure, resulting in costly repairs and downtime.
12x22x7 oil seal
In the realm of trustworthiness, it is important to rely on reputable manufacturers who guarantee quality through rigorous testing and industry certifications. Trusted brands often subject their oil seals to stringent quality control processes to ensure they meet the highest standards. When selecting an oil seal, opting for products from well-established manufacturers can provide peace of mind regarding the product's reliability and performance.
An equally crucial aspect is the installation process. Improper installation can cause immediate damage to the seal or lead to leakage issues over time. Utilizing installation tools specifically designed for oil seals can prevent damage during the fitting process. Ensuring the shaft and bore are clean and free from debris is essential to avoid compromising the seal's effectiveness.
Moreover, routine inspections are advisable to preempt any potential issues with the seals. Regularly checking for signs of wear or damage can prevent unexpected machine failures. In sectors where machinery uptime is critical, such as in manufacturing or automotive industries, incorporating proactive maintenance strategies around components like oil seals can significantly improve operational efficiency and reduce costs.
In conclusion, the 12x22x7 oil seal, though small, is a critical component that requires careful consideration regarding its material composition, manufacturer credibility, and installation. Leveraging extensive expertise and understanding the authoritative practices in oil seal usage can not only enhance machinery performance but also safeguard against unexpected downtimes. For businesses relying on mechanical operations, investing time and resources in selecting the right oil seal can offer substantial long-term benefits.